PEAK is a leading sportswear brand, established in China in 1989. In 2015, PEAK’s revenue surpassed 3 billion RMB. Two years later, PEAK became one of the pioneers in making shoes using 3D printing. By November 2021, PEAK’s lightweight basketball shoes series, TaiChi, released a 3D-printed shoe. Its upper is printed with thermal-sensitive material that changes color according to variations in temperature. In December 2021, PEAK released the first version of its 3D printed sneaker series, Future Fusion 3.0xSeapool, with a limited run of 199 pairs. Today, PEAK is a giant with more than 5,000 retail stores in China.
For years, PEAK has embraced 3D printing technology in its footwear manufacturing process. Thanks to this innovation, PEAK’s release of 3D-printed sports shoes has intensified and the improvements that 3D printing has brought to PEAK products are evident.
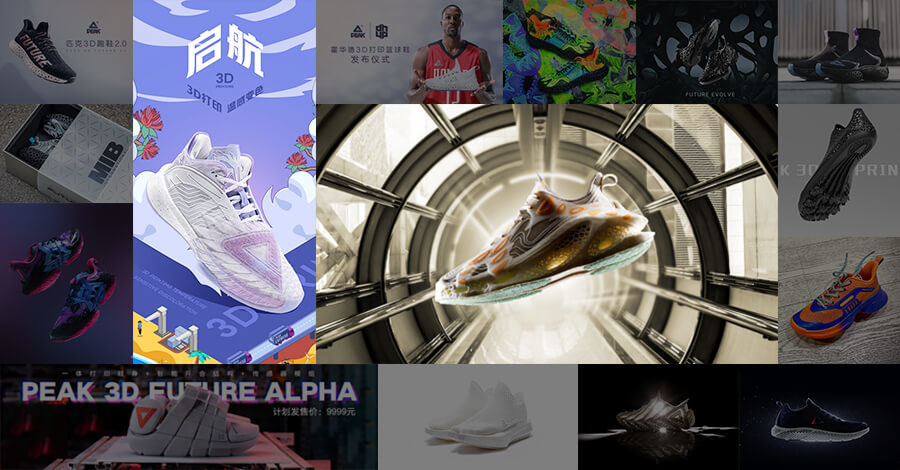
Posters of Various PEAK 3D Printing Sports Footwear
Rebirth rather than Refurbished
PEAK rebuilt its manufacturing process from the bottom up around the process of 3D printing. For example, Future Fusion 3.0xSeapool has a shoe upper fabricated using Raise3D FFF (Fused Filament Fabrication) technology. This shoe upper is directly formed by successively depositing multiple printed layers using an FFF printer. For each layer, the FFF printer uses a colored material as a thread with 0.4-0.8 mm in diameter, following a crossed path which forms a pre-determined grid pattern. Therefore, the FFF printer can draw each layer with a different pattern and color. As the FFF printer builds layers on previous layers, it forms a composite fabric that is permeable, with a unique, creative appearance, permeability, and unlimited combinations.
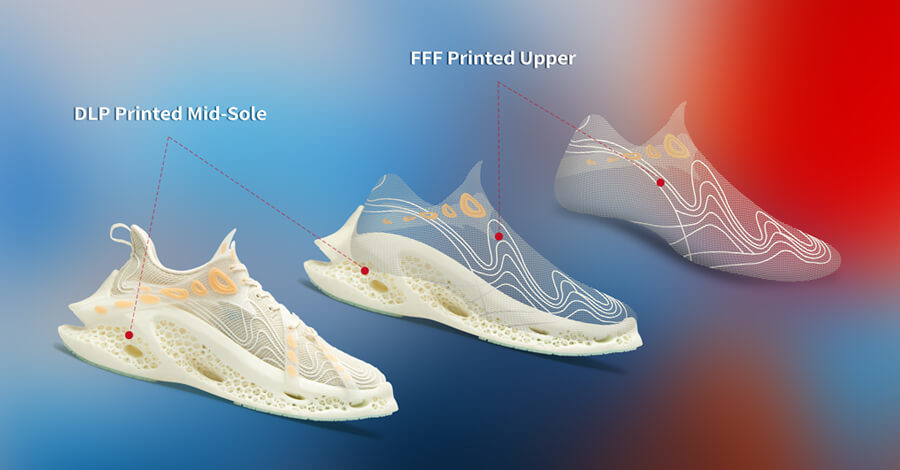
Structure of Future Fusion 3.0
Based on this method of fabrication, PEAK rethought its sneaker production process, resulting in a procedure based on 3D printing that is shorter and more flexible than the original manufacturing process. The most significant improvement is the shoe upper fabrication phase. Through an integrated FFF printing solution, PEAK replaced the eight original flyknit procedures with three new procedures. Due to the high level of digitalization of the FFF printing process, these new procedures are much more efficient when it comes to variable quantities and product demand. Compared with the flyknit process, initiating a new printing line does not need a huge amount of labor to program a sophisticated weaving path. Instead, 3D printing software automatically generates printing paths and a corresponding machine command code. Additionally, a 3D printer is much easier to calibrate for material loading and unloading, and without the need for tool changing, and can deliver shoe uppers with any pattern or combination following a pre-determined printing path. Furthermore, these features bring huge advantages to the prototyping stage thanks to reduced costs and time cycle. Due to this automation and digitalization, 3D printing allows for the rapid prototyping of functional shoe uppers and midsoles that can be directly assembled and worn. This process enables PEAK to carry out more design iterations that are also quicker.
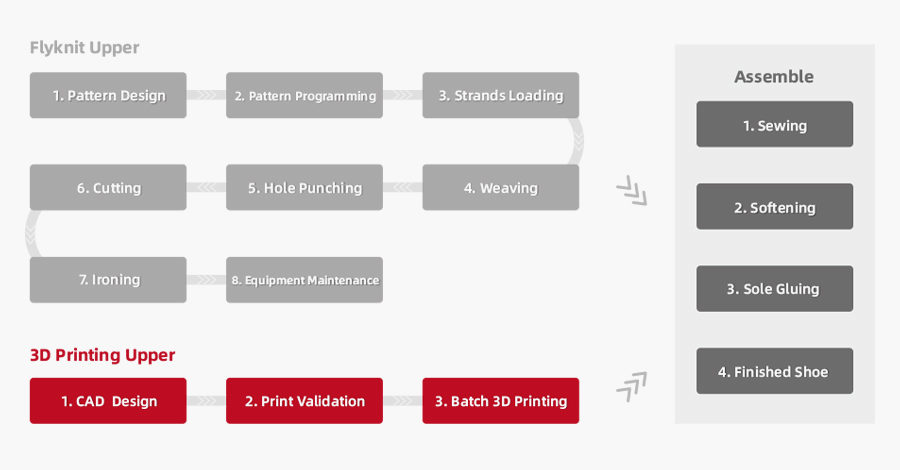
Comparison of Flyknit and 3D Printing Process
Quick Launch with Flexible Shoe Upper Manufacturing
The batch production of 199 pairs of Future Fusion3.0xSeapool had a rapid initiation and lead time. Once the CAD design is confirmed, the 3D printing manufacturing phase can start immediately and seamlessly. Before the 3D printer begins operating, an engineer needs to import the confirmed CAD file (exported to 3D printable format, for example, STL format) into ideaMaker. This file is then “sliced” or turned into a computed command code (better known as a .gcode file), which in turn is uploaded to the 3D printer. This procedure only takes a few minutes.
Afterwards, the fabrication and assembly process only require ten workdays. Sneaker uppers and midsoles are 3D printed simultaneously over the course of four days by two distinct 3D printing technologies. It takes two days to gather all the 3D printed components and another three days to queue and go through the assembly process.
As an example, sneaker uppers are printed by the Raise3D specialized footwear printing solution, which delivers single pair of sneaker uppers in about three hours. There is no need to adjust the printing procedure since the various shoe sizes of uppers are included in the task queue. The multiple printers working synchronously require little labor, and the 199 pairs of uppers are finished in four days.
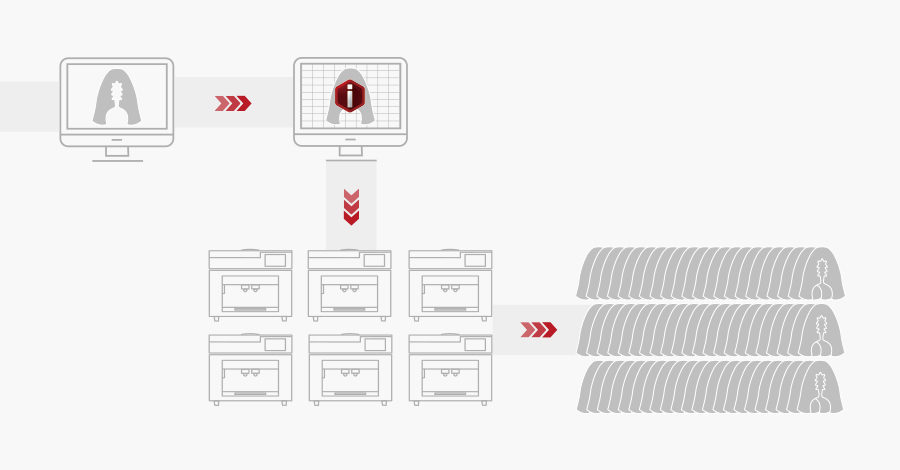
FFF Printing Process of Upper
3D printing signifies a much lower production cost per unit for small batch production. With the traditional process, the mass production of shoe uppers can only be achieved with streamlined knitting and cutting. The cost structure of this type of process is not suitable for small batch production. It requires an extremely high investment of around 25000 USD to purchase a single set of knitting and cutting equipment. A high quantity of material is required for each processing round to break even with the depreciation of the machine and tool cost. Therefore, fabricating 199 pairs of shoe uppers with this type of equipment would result in heavy losses or unreasonably high prices. However, the Raise3D printing technology adopted by PEAK is economical and capable of producing any needed quantity of uppers, therefore no sunk cost or high depreciation is generated. Furthermore, with 3D printing technology increasing in the future, production cost-efficiency will most likely improve even further.
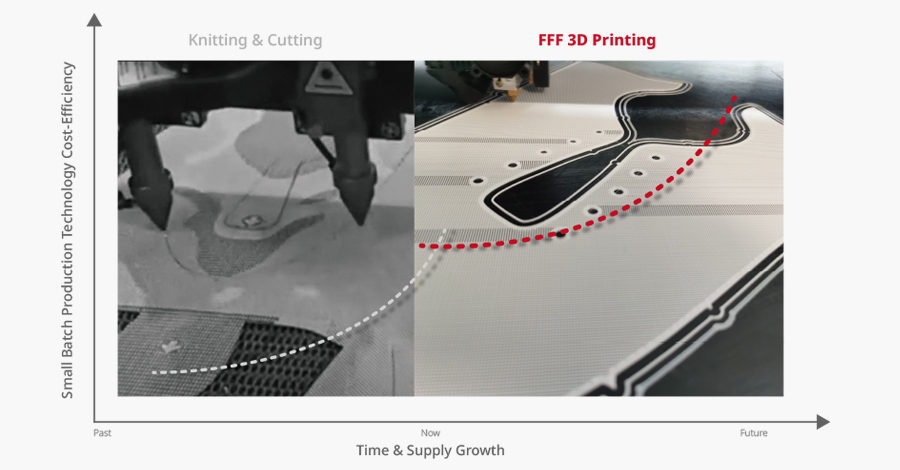
Trend of Small Batch Production Technology Cost-Efficiency
All this makes it quite distinct from major manufacturing scenarios in terms of time and cost, but this is what flexible manufacturing is all about.
PEAK’s Evolution of 3D Printed Sneaker
The market witnessed PEAK’s efforts and subsequent success in implementing manufacturing using 3D printing. Starting with the Future series, PEAK expanded the 3D printing family with the Future Fusion series, Future E and Future Alpha. Among these, the Future Fusion series continues to evolve, reaching Future Fusion 3.0 today. Moreover, PEAK brought 3D printing to the TaiChi series, its star product. In the company’s history of implementing 3D printing, PEAK employed different printing technologies as well as new business strategies. From its history of experimentation with different 3D printing technologies, PEAK recognized that FFF technology is more cost-effective for batch production and can print using flexible materials, a required property of shoe uppers. An example of a flexible material that can be printed by an FFF printer and meets the shoe uppers flexibility requirements is TPU (Thermoplastic Polyurethane). A 3D-printed flat shoe upper is flexible and can be bended and assembled. This method avoids the downside of having to print an overhang support structure, thus making the print more efficient. Such integration contributes to PEAK’s deep research into 3D printing mechanisms and manufacturing applications.
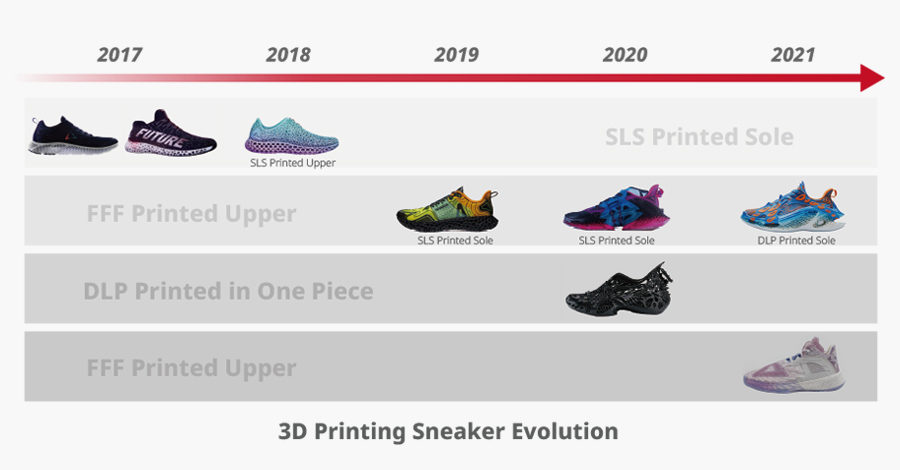
Evolution of PEAK 3D Printing Sneaks
The Future Fusion series is evolving at a product and manufacturing level by making the most of 3D printing. When comparing the 3.0 version with the 2.0 version, the former not only has design breakthroughs such as detachable shoe upper accessories but also improvements in the manufacturing cost-efficiency. Its manufacturing adopts Raise3D footwear printing technology to enhance the qualification ratio, printing precision, and surface quality. This is contributed to years of practice and research by PEAK, who identified several critical criteria, including printing speed, integration between hardware and software, stringing control, and positioning precision. Raise3D’s solutions provided optimized FFF printing technology for PEAK, fulfilling these criteria.
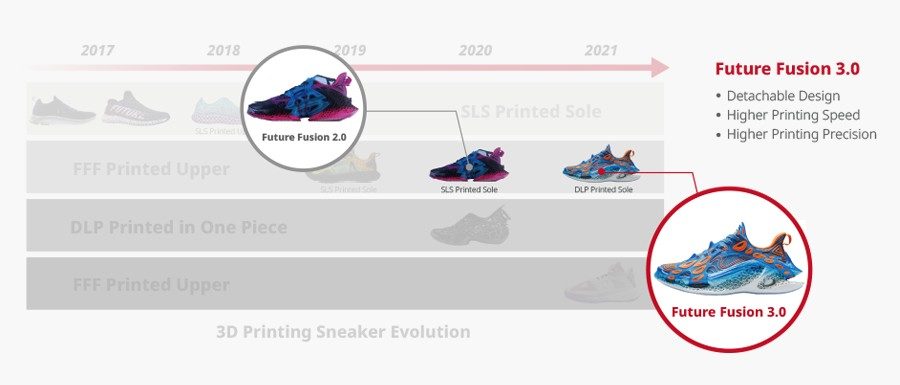
Improvement of Future Fusion 3.0 using Raise3D Printing Technology
The footwear industry’s transformation towards the 3D printing process needs support from technology suppliers capable proving the full solution. To implement flexible manufacturing, manufacturers must integrate digitalization, materials, and the machinery. Once there are manufacturers eager and focused on 3D printing implementation like PEAK, the capability of Raise3D’s FFF solution will be their strongest ally.