Mideco, an Australian-owned company established in 1950, specializes in providing dust control products and solutions for mines, quarries, and various commercial environments. Mideco brings together generations of expertise and an outstanding capacity to deliver tailored industrial dust collection solutions to protect the health and safety of thousands of employees. With over 70 years of expertise in dust collection projects, Mideco has a strong track record in solving complex dust collection and extraction system challenges.
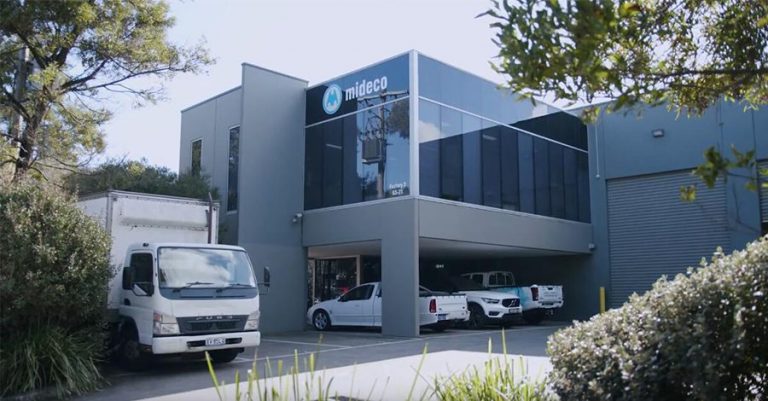
Mideco has been delivering tailored industrial dust collection solutions since 1950.
Challenges
Mideco faced a challenge in the form of optimizing its product development process, which involved designing intricate parts, prototyping, and collaborating with suppliers. Traditional methods were time-consuming and expensive.
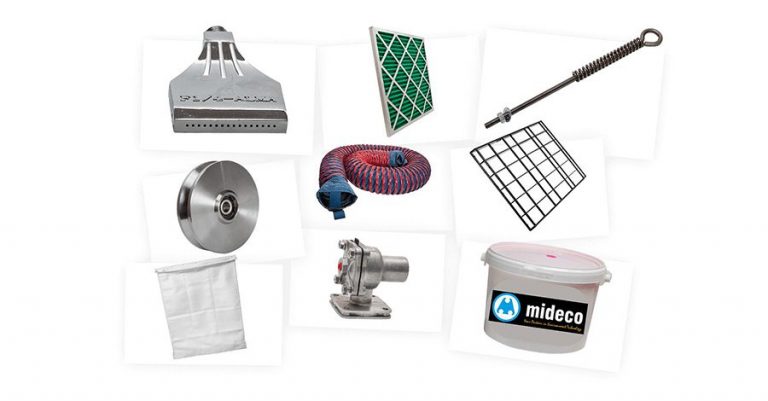
Mideco faced the challenge of optimizing its product development process.
Bring Intricate Designs to Life with Incredible Accuracy
Mideco took a path that led them to 3D printing, in order to solve the traditional time-consuming and high-expense issues. This proved to be a massive benefit when designing intricate parts and prototyping during the product development process.
After their evaluation and comparison of offers within the 3D printing industry, Mideco adopted the Raise3D Pro3 Plus 3D printer. The exceptional precision and accuracy of highly detailed prints printed by Raise3D Pro3 Plus allowed Mideco to bring intricate designs to life with incredible accuracy, significantly benefiting their product development process.
Mideco’s team appreciated the remarkable reliability, robust construction and stable performance demonstrated by Raise3D’s Pro3 Plus printers. During long and complex print jobs, Mideco also got consistently exceptional results with this model.
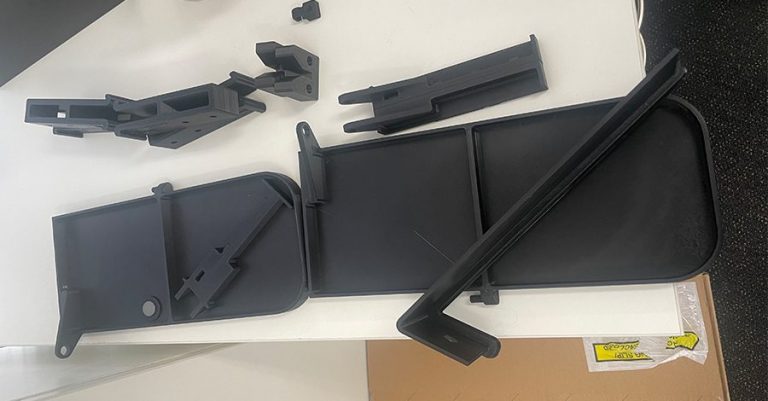
Mideco got consistently delivering exceptional results during long and complex print jobs.
Significant Improvements of Labor and Production Costs
Mideco reduced labor costs by 50% during the production process, making their operations more efficient and cost-effective. The Raise3D Pro3 Plus is a game-changer in streamlining their product development process. Depending on the size of the part, production costs were reduced by approximately 30%, further enhancing their competitiveness in the market.
Before implementing the Raise3D Pro3 Plus, Mideco’s product development process involved having designers create a 3D model, sending the design to a supplier to create a sample, and dealing with extended lead times and high labor costs.
The introduction of 3D printing using the Raise3D Pro3 Plus brought about significant improvements. Instead of sending the design to the supplier, they can import 3D models into Raise3D’s Slicer Software – ideaMaker – and 3D-print it on the Raise3D Pro3 Plus. This way, prototyping and part production lead times were significantly reduced, resulting in cost savings throughout the design-to-production process.
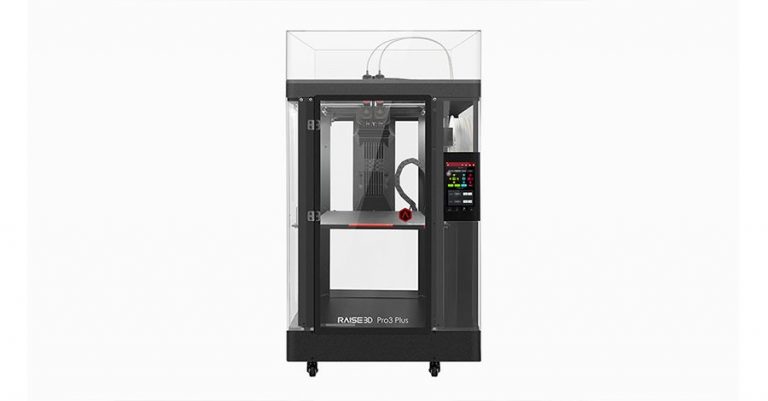
Significant improvements brought about by using Raise3D Pro3 Plus.
Future Possibilities
In conclusion, adopting the Raise3D Pro3 Plus 3D printer has revolutionized Mideco’s product development process, leading to increased efficiency, cost savings, and enhanced precision. This success story showcases the transformative potential of 3D printing technology in various industries, including environmental engineering and sustainability.
Professionals in environmental engineering and sustainability can explore 3D printing applications related to recycling and sustainable materials. Some are already utilizing 3D printing to recycle plastic waste into usable products, aligning with the principles of environmental sustainability.
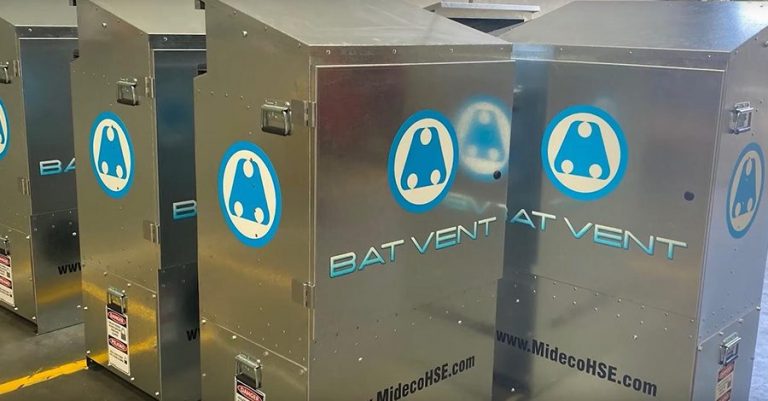
Professionals in environmental engineering and sustainability can explore 3D printing applications.
This case is shared by Bilby 3D, which is Raise3D’s reseller in Australia.