Based in Milan in Northern Italy, Model Makers Milano specializes in creating models and prototypes for shipyards, designers and architects, with the best made-in-Italy quality. They were able to accelerate their production times thanks to the use of Raise3D Pro2 Plus printers, in addition to making the process more reliable.
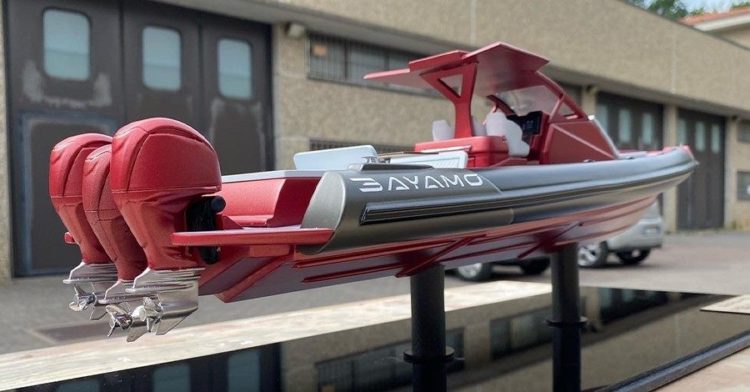
Model Makers Milano were able to accelerate their production times thanks to the use of Raise3D Pro2 Plus printers
According to the CEO, senior maker and painter, Jacopo Daniele Molfese, the mission of the company is to « turn your idea into a tangible object, going over the simple rendering. We build scale models and prototypes, using a big range of cutting-edge technologies. From CNC milling to FFF, SLS or SLA additive processes. You have just to choose, the rest is just our kind of magic. »
Before the advent of 3D printing, Jacopo had to prepare everything by hand using traditional manufacturing tools. The whole process was not only time-consuming but also very expensive. To create replicas of the same model manually, he had to work with wood and resin glass.
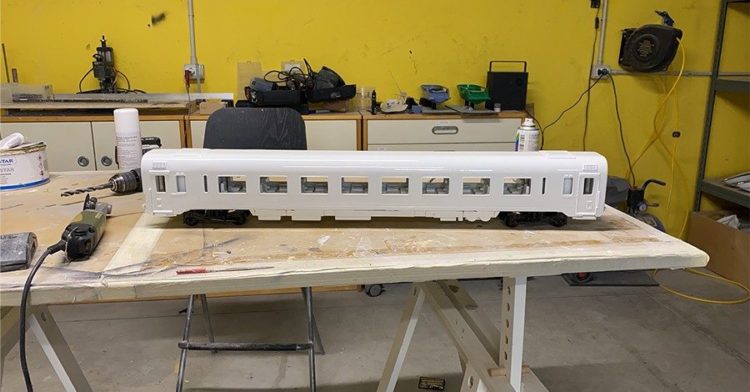
Model Makers Milano build scale models and prototypes, using a big range of cutting-edge technologies
Jacopo’s first encounter with 3D printing was in 2014, and he immediately recognized its potential. With this technology, he could offer a greater variety of models, instead of concentrating on just one design, and also work faster, thereby saving time and money.
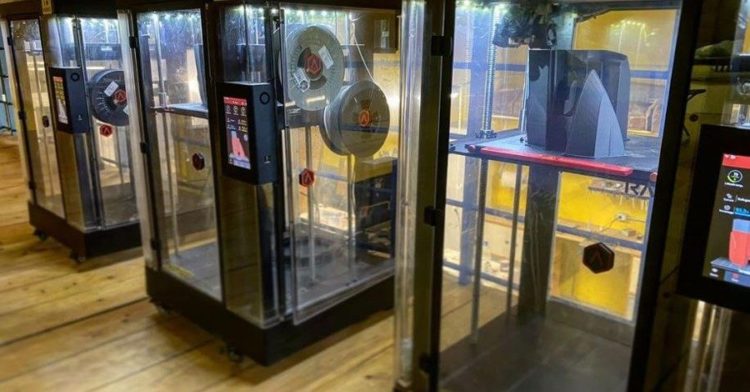
With 3D printing technology, Jacopo could offer a greater variety of models
His association with Raise3D began when he started working in a modelling and prototyping laboratory. When he decided to start his own business, he chose Raise3D to be part of his 3D printer portfolio. Jacopo opted for Raise3D because he was seeking a professional 3D printer that offered high quality, catered to prosumers, and most importantly, had a large Z-axis.
The final choice was the Raise3D Pro2 Plus since he wanted a 3D printer that « expanded in height; in fact, once customers started to ask for bigger models (around 1 meter), I realized that a ‘taller’ printer could allow the model to be ‘cut’ into fewer pieces. »
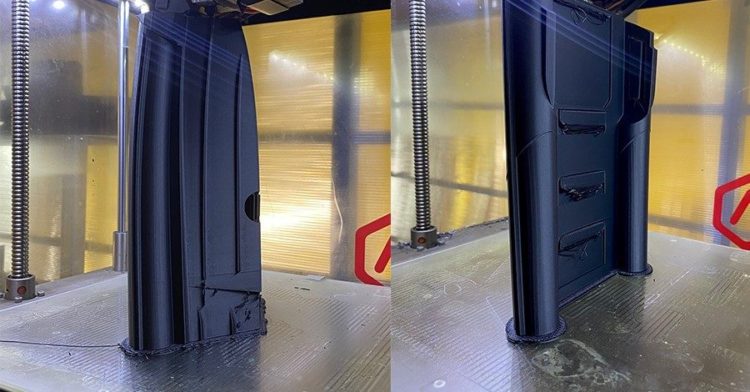
Raise3D Pro2 Plus is a 3D printer that expanded in height
Raise3D significantly helped to reduce production times. With three Pro2 Plus printers, Jacopo managed to reduce manufacturing times to one-third of what they were before. The process is now faster and more reliable, and Jacopo trusts his 3D printers so fully that he is confident he can leave the printers alone and that the printing process will be successfully complete by the time he checks it personally. Furthermore, the high print quality has reduced post-processing time significantly.
At Model Makers Milano, the team primarily works with ABS, using it to print semi-finished products. The choice of ABS is based on its ability to withstand high temperatures, as some models are exposed in nautical saloons during the summer. Additionally, ABS ensures that the printed parts are not only aesthetically pleasing but also durable with articulated joints and small movements.
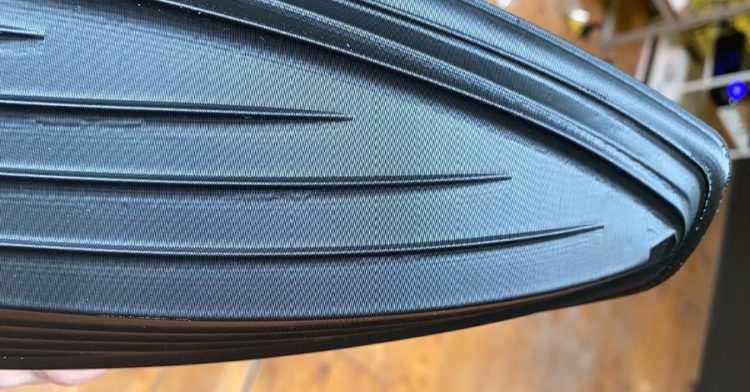
Model Makers Milano build scale models and prototypes, using a big range of cutting-edge technologies
To handle slicing and monitor and check the STL model with high accuracy, Jacopo uses ideaMaker, which he finds easy, intuitive, and user-friendly.
Satisfied with the professional quality and appearance of the Raise3D printers, Jacopo’s customers are impressed when they visit his laboratory. Jacopo plans to update his 3D printer fleet as his business grows. Though unsure of the specific direction his business will take, one thing he is sure about is that Raise3D will continue to be by his side.
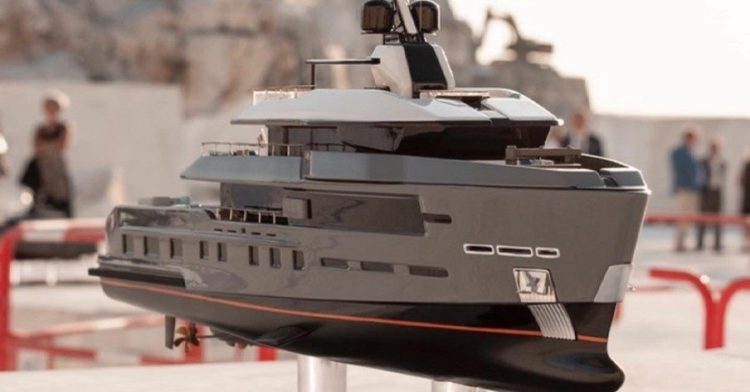
Jacopo is satisfied with the professional quality and appearance of the Raise3D printers
This case study was provided by Ciano Shapes, the Raise3D Sales Partner in Italy. If you are located in Italy and require assistance with your own project, you can visit Ciano Shapes’ website or reach out to them via email at info@cianoshapes.com