Advantech is a globally renowned industrial Internet of Things (IoT) provider with operations spanning across 28 countries and approximately 8,900 employees worldwide. 2023 marks the 40th anniversary of Advantech’s establishment and the 23rd anniversary of its presence in Kunshan, Jiangsu. As a practitioner and enabler in the field of IoT, Advantech has made significant investments in the construction of digital factories in recent years. Not only do they leverage their own AIoT technologies, but they also actively incorporate external innovative technologies, with 3D printing being one of them.
Within Advantech’s manufacturing processes, there is a substantial demand for customized, non-standard components, namely PCB positioning fixtures. Historically, these fixtures were primarily outsourced and manufactured using dielectric materials, processed through CNC machining. However, over time, issues with the CNC outsourcing process began to accumulate.
Challenges Faced Amidst the Rising Trend of Increasing Machining Costs
First, machining costs are continually on the rise. As the economic influence of Shanghai continues to expand, the cost of living, including housing and general expenses, in Kunshan has steadily increased. Simultaneously, experienced CNC operators are dwindling in numbers, and there is a decreasing pool of young talent willing to pursue CNC machining as a career. These factors have led to a year-on-year increase in CNC machining costs in recent years.
Second, outsourced production tends to have long production lead times, typically ranging from 1 to 2 weeks. This can pose a significant challenge when facing customer demands that require swift responses, potentially affecting delivery schedules.
Third, flexibility is limited in traditional outsourcing arrangements. Once the drawings are submitted, making changes becomes cumbersome and inflexible. This lack of flexibility hampers the ability to adapt to iterative product designs. In cases of urgent requirements with frequent design changes, the only option is often to restart the production process.
Changing the Mindset: Leveraging 3D Printing Technology
In the face of these challenges and difficulties, Mr. Li, the manager of MPM at Advantech’s Kunshan factory, has been actively seeking new technologies and solutions for improvement. During a technical exchange with colleagues from the headquarters, the issue was raised, and at that time, his colleagues from the headquarters recommended 3D printing technology.
After conducting a comprehensive comparison of several 3D printing devices, Advantech acquired the Raise3D Pro2 Plus. Mr. Li expressed his satisfaction with this decision, saying, „At the time, someone recommended another foreign printer to me, but we conducted extensive research and ultimately chose the Raise3D Pro2 Plus.“ He further elaborated on the reasons for this choice, stating:
„First, it’s about precision. We conducted multiple rounds of sample testing and internal comparisons, and what pleasantly surprised us was the high precision of the Raise3D Pro2 Plus.“
„While ensuring precision, the printer has a large build volume. Although most of our fixtures are relatively small, typically under 20cm in size, occasionally we need to produce larger components. With dimensions of 305×305×605 mm, the Raise3D Pro2 Plus offers ample space to meet these manufacturing needs without requiring a significant additional investment. This makes it highly cost-effective.“
„Furthermore, there are many thoughtful details in this 3D printer. As I mentioned, it incorporates a lot of design logic tailored for manufacturing enterprises. We see features like external components such as lead screws, nozzles, and cable chains, as well as internal elements like RaiseCloud, a cloud management platform that can manage multiple printers as a team, and software like ideaMaker, which is offline, closed, and secure for slicing. Even the weight of the Pro2 Plus is surprising; it’s hard to believe that such a compact desktop machine weighs as much as 50kg.“
3D Printing 90% of Positioning Fixtures Easily Reduces Costs and Increases the Efficiency of Manufactured Parts
„The Raise3D Pro2 Plus is placed inside the engineering workspace of the factory, offering straightforward operation. Our engineers are proficient in software such as UG and SW, allowing them to quickly adapt to its operation. Previously, outsourcing CNC machining meant it took 2 weeks to receive components. However, with the adoption of the Raise3D Pro2 Plus, our production speed has significantly improved. Even for larger components, we can now manufacture them in just 20 hours, requiring no additional surface treatment, which has proven to be more than sufficient.“
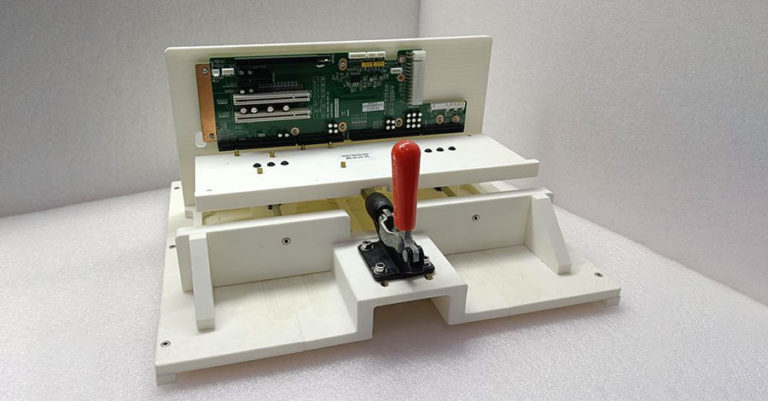
PCBA Assembly Positioning Fixture Printed with Raise3D Pro2 Plus
In terms of materials, we currently primarily use PLA, which is more cost-effective compared to the previously used dielectric materials. Typically, we fill the PLA with 30% or 50% infill and use ideaMaker to adjust it to a solid structure only where strength is required. Achieving a low weight without compromising structural integrity significantly enhances material utilization rates, leading to substantial cost reductions. Consequently, the overall fixture cost is approximately 10% of what it used to be.“
Optimizing cost efficiency through innovative technology while maintaining high reliability is the reason why companies like Advantech, Schaeffler, and SKF Industrial Technology have chosen Raise3D as their brand of choice for professional-grade 3D printers.