It’s well-known that 3D printing allows for design innovation and manufacturing flexibility that would not be possible through conventional production methods. However, while these benefits of 3D printing technology have resulted in shifts across engineering and manufacturing industries, the influence of 3D printing in biotechnology remains in its infancy, with likely only a small fraction of its potential being realized.
Now, this trajectory is changing. Innovators in in the health sciences are rapidly developing creative applications that introduce the fundamental capabilities of 3D to research and experimentation with organic material.
Led by Bioengineering Ph.D. student Ralf Zgeib, the Stevens Institute of Technology in Hoboken, NJ has used Raise3D print technology to drive a truly creative solution at the crossroads of 3D printing and biotech.
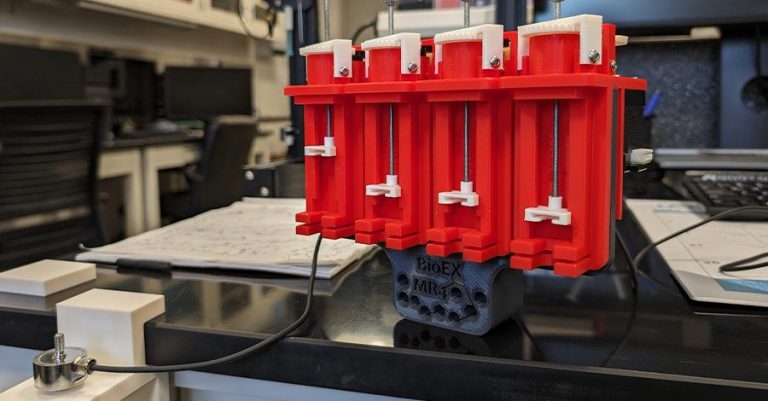
Stevens Institute used Raise3D print technology to drive a truly creative solution at the crossroads of 3D printing and biotech.
The Challenge
The laboratory at Stevens sought a method to replicate the speed and flexibility of 3D printing with the challenge of working with sensitive biomaterials. Conventional 3D printers have material limitations, using synthetics in the form of filaments and resins. The objective for the Stevens Institute was not only to successfully fabricate original models from extremely precise design parameters, as made possible by additive manufacturing, but to achieve this using living tissues.
3D Printing a 3D Bioprinter
To achieve their goal of printing living tissue, Zgeib envisioned a bioprinter that didn’t yet exist. The team at Stevens decided that the first step in the process would be to utilize one tool to create another: In other words, use a 3D printer to print a 3D printer.
“We work on developing low-cost bioprinters with multiple material functionalities,” Zgeib explains. Leveraging his prior expertise in 3D printing (which involved – at one point – 3D chocolate printing), they developed a custom extrusion head made entirely of 3D-printed parts on the Raise3D Pro3. This extrusion head, when integrated with laboratory-grade components, allowed for multiple material extrusion that fit the specific criteria necessary in working with organic tissue.
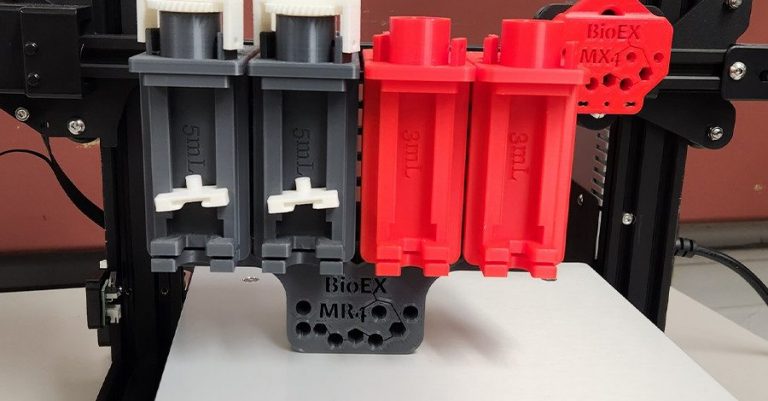
A custom extrusion head made entirely of 3D-printed parts on the Raise3D Pro3.
“Our printer enables us to print tissues with multiple cell types in a single process,” Zgeib notes.
The ability to fabricate complex biological constructs with precision and efficiency has the potential to revolutionize tissue engineering research and advancement.
Bioprinting: Implementation and Impact
The Stevens Institute team collaborated with medical professionals and hospitals to translate their research into practical applications. For example, they partnered with a medical university hospital to study placenta diseases by modeling miniature placentas and testing different biomolecules and medications.
Zgeib emphasizes the importance of collaboration in driving innovation. “We work with hospitals and doctors to develop solutions tailored to their specific applications,” he states.
This collaborative approach ensures that their research addresses real-world medical challenges.
As a complement to bioprinting technology, the Institute is exploring other biomanufacturing techniques like melt-electro writing. This multidisciplinary approach allows them to explore diverse avenues in tissue engineering and regenerative medicine that have far-reaching implications in health sciences.
“Our ultimate goal is to print tissues and organs for transplantation,” Zgeib shares.
While the Steven’s Institute team currently focuses on research and development, their long-term vision involves contributing to advancements in regenerative medicine. They aim to demonstrate practical applications of their bioprinting technology. “We prototype and test different designs, ensuring that our solutions are viable for real-world use,” says Zgeib.
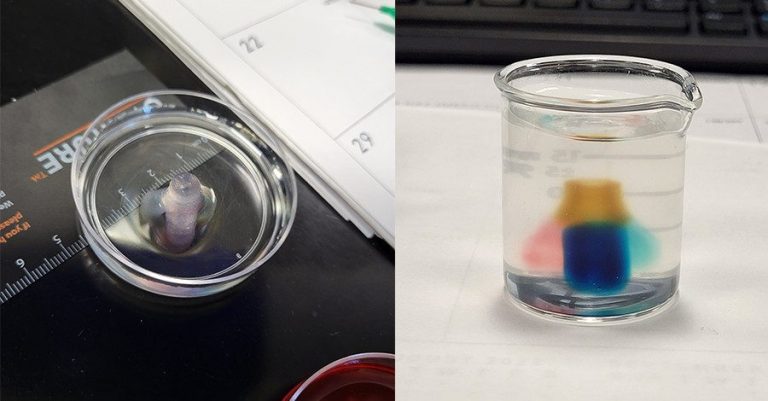
The Stevens Institute team collaborated with medical professionals and hospitals to translate their research into practical applications.
3D Printing Overcomes Both Technical Challenges and Budget Constraints
Zgeib recalls the technical challenges faced during the development process. “Until we used the Raise3D Pro3, we couldn’t achieve functional parts due to issues like warping and poor tolerances,” he explains.
The printer’s smooth motion and precise control mechanisms were instrumental in overcoming these hurdles.
Despite budget limitations, Zgeib’s team maximized the capabilities of their resources. “We started with the basic Raise3D Pro3 printer, which has been working perfectly for us,” he says.
The team’s focus on using creative thinking to develop cost-effective solutions enabled them to achieve remarkable results within constrained budgets.
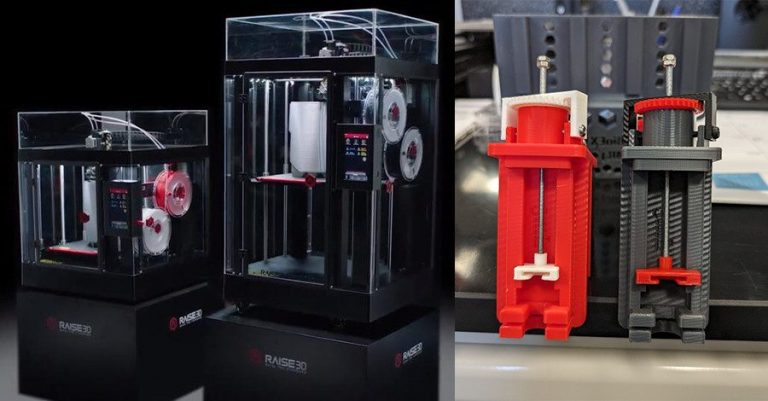
Functional parts of 3D-printed parts on the Raise3D Pro3.
Fueling Innovation for the Future
Zgeib’s lab actively contributes to knowledge dissemination in the field of additive biomanufacturing. “We collaborate with organizations like ASME, showcasing our research and sharing insights with the broader scientific community,” he says.
Zgeib’s journey from running his own 3D printing business to pursuing a Ph.D. in bioengineering serves as inspiration to aspiring researchers. “We want to inspire the next generation of engineers and scientists to push the boundaries of what’s possible.”
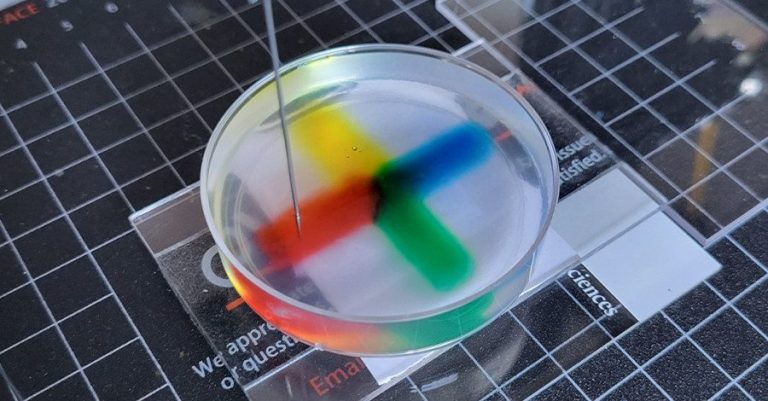
Zgeib’s inspiration to aspiring researchers.
Looking Forward
The Stevens Institute’s work in developing custom bioprinting solutions has contributed to the advancement of research in tissue engineering while holding a promise for real-world advances in the practice of medicine. With continued collaboration, innovation, and dedication, these types of creatively designed applications are poised to make significant contributions to regenerative medicine and biotechnology in the years to come.
As Zgeib nears the completion of his Ph.D., he looks forward to exploring new frontiers in tissue engineering and regenerative medicine. “There’s still so much to discover and innovate in this field.”