3D printing is a versatile form of additive manufacturing that is becoming widely adopted in various fields. It is currently being introduced into the design and development of plastic surgery and orthopedic medical devices and equipment. Due to its sustainability and efficient use of time in the production stage, 3D printing brings improvements to the manufacturing of medical devices. The impact of 3D printing can be seen in the collaborative work of CREA3D and Dr. Valenti, a podiatrist. Their work combines 3D printing with other digital technologies to provide patients with internal design and tailor-made insoles and orthotics, thereby improving the effectiveness of auxiliary treatment and the efficiency of daily management.
Dr. Mirko Valenti introduced 3D printing technology to treat clinical cases of posterior tibial tenosynovitis with conservative corrective therapy. Dr. Valenti’s introduction of 3D printing was both innovative and highly effective. Dr. Mirko Valenti purchased Raise3D’s E2 3D printer equipped with IDEX (independent dual extruder) technology for his studio. As an IDEX 3D printer, the E2 is ideal for printing a pair of orthopedic insoles at the same time.
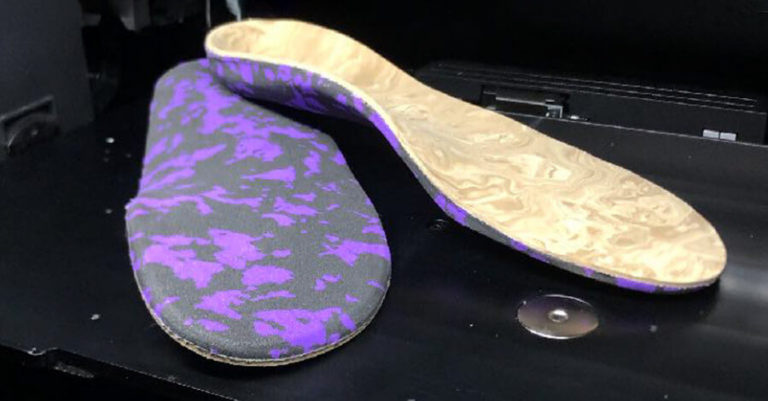
Crea3D combines 3D printing with other digital technologies to provide patients with tailor-made orthopedic insoles.
Insole Production Before 3D Printing
Each pair of orthopedic insoles is specific to each patient because each patient has different needs. Therefore, the mechanical properties of different parts of the insoles need to be customized according to the patient’s condition.
This proved to be a challenge for the traditional process of orthopedic insoles. In the traditional process of producing custom insoles, a CNC machine must be used to mill a piece of material to obtain the desired insole shape. A high-precision CNC machine and a great deal of manpower are required to ensure the accuracy of the anatomical area in the insole. Achieving this is a time-consuming and complex process. The traditional method generates debris and dust during the production process, polluting the working environment and endangering the health of workers.
Insole Production After 3D Printing
Abandoning traditional CAD-CAM machines, Dr. Mirko Valenti prints his orthotic insoles with PP filament because its durability and strength provide better support for the patient’s foot. Printing a pair of orthopedic insoles with PP filament is a simple process.
First, Dr. Mirko Valenti scans the patient’s foot. Then he uses CAD tools to make the model of the orthopedic insoles compensate for the affected area, ensuring that the arch is supported and the heel is stable. Dr. Mirko Valenti then uploads the file of the model to the 3D slicing software ideaMaker, to optimize mechanical properties, such as changing the shape and percentage of the infill of the model during slicing. For example, a honeycomb infill pattern can make the entire structure rigid. The infill allows the user to obtain different results in terms of the deformability and mildness of the orthosis. After Dr. Mirko Valenti uploads the model file to the 3D printer remotely, the E2 IDEX 3D printer prints a pair of insoles at the same time. Finally, Dr. Mirko Valenti wraps the sole with EVA or other specific materials suitable for skin contact.
This entire manufacturing process from the scanning, design, and manufacturing stages, is completed in less than 24 hours.
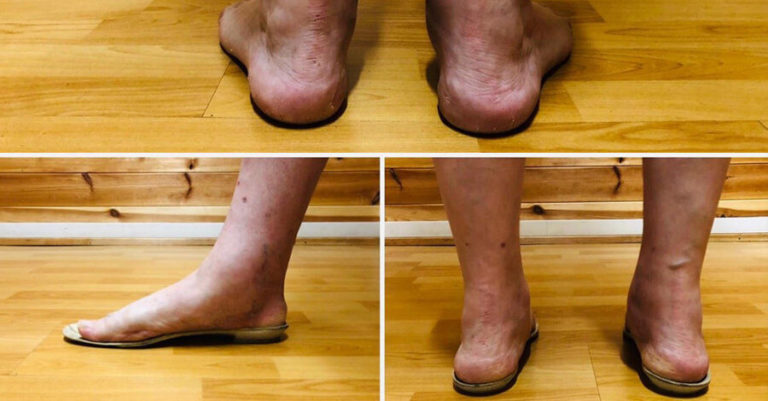
3D printing has great advantages for personalized patient orthopedic insoles.
The Benefits of 3D Printing Orthopedic Insoles
3D printing simplifies the traditional work process and shortens the production cycle and delivery time. The 3D printed model can be formed in a single process without using any other additional machinery and tools. It only takes 2-3 hours to print a pair of orthopedic insoles on a Raise3D E2 printer, and the whole process is automatically operated without the need for manual operation. Producing insoles without 3D printing requires a large number of manual instruments and it takes longer to correctly obtain an accurate model of the anatomical area to be focused. Dr. Mirko Valenti’s implementation of 3D printing shows that a successful personalized orthopedic treatment method can be created using 3D printing.
3D Printing is An Efficient Production Process
3D printing is a more efficient process for producing insoles. Users can design models in a centralized manner and mass-produce them at the same time. With 3D printing, there is no need for multiple design-verification-modification processes. Since 3D printing gives the user the ability to produce small batches of custom parts on-demand, recipients can get the model the first time, and reduce the time spent on delivery.
Enclosed 3D Printers Lead to a Healthier Work Environment
Enclosed 3D printers such as those from Raise3D, filter any of the fumes released from the heating 3D printing material. This reduces the need for large workshops or restrictive production environments. As a result, 3D printing provides a cleaner and healthier environment where users can perform mass production in an office setting.
The Benefits of the Right 3D Printing Software
Dr. Valenti chose polypropylene as the 3D printing material to provide support and flexibility for various corrective elements of the insole. Each filament performs better under different parameters. The right 3D printing software can streamline this work considerably.
For example, ideaMaker is a 3D slicing software that has a variety of built-in preset templates for different filaments (including Polypropylene).
The main benefit is that users can customize the parameter for the internal structure, such as the infill density, infill angle, etc. to control the mechanical property.
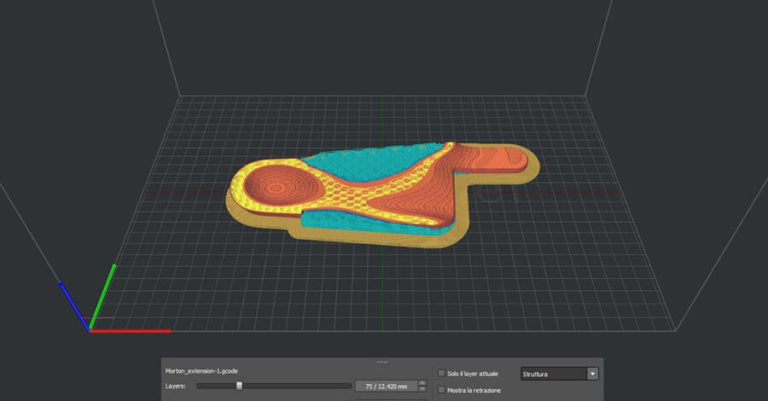
Adjust the mechanical properties of the model when using ideaMaker to slice the model.
Raise3D assists the entire production process of orthopedic insoles
Dr. Valenti chose Raise3D’s E2 desktop 3D printer to complete the production of the orthopedic insole. As a medium-sized professional desktop printer, the E2 can fully meet most of the print quality requirements, while suitable for home and small studio environments. The IDEX technology of the E2 allows users to produce a pair of orthopedic insoles at the same time, which can maximize production efficiency. In addition, during the manufacturing process, Dr. Valenti uses ideaMaker 3D slicing software to strengthen the internal structure of the insole. ideaMaker provides parameter settings and a variety of filament templates, allowing users to customize and modify the mechanical properties of the orthopedic insole. The E2 desktop 3D printer supports various filaments including polypropylene. Users can learn about the characteristics of the filaments and download the relevant model files here.
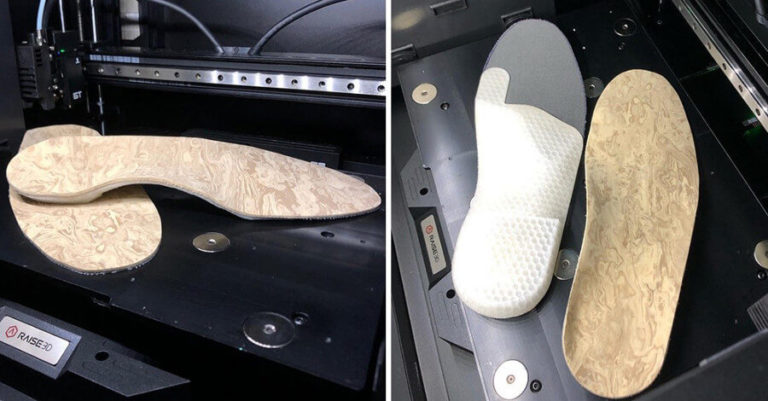
Raise3D ecological chain products help the entire production process of orthopedic insoles.
3D printing will benefit more medical fields
3D printing provides better customization, precision, aesthetic appearance, and lightweight structure. It also greatly shortens the manufacturing process, timeline, and makes it easier to maintain patient data. Dr. Mirko Valenti used 3D printing for podiatric therapy based on plantar orthoses. He utilized Raise3D printers and 3D printing software to complete the integrated manufacturing process of orthopedic insoles, demonstrating the superb capabilities and efficiency of Raise3D products and services. The Raise3D ecosystem is utilized during the entire design, verification, and production process of the model for plastic surgery and orthopedic auxiliary, greatly improving production efficiency.
This case is provided by Raise3D’s Italian distributor, Crea3D.