HTI Technologies, a leading provider of medical and industrial components, transformed their fixture production process by switching from CNC and FFF printing to Raise3D’s DF2 true DLP solution. With precision down to 0.05 mm and print times reduced from 10 hours to under 3, HTI accelerated validation, cut costs, and improved flexibility—all while maintaining industrial-grade quality.
Application: Laser Marking Jig
“I was able to reduce the iteration time from 10 hours to just 2 hours and 40 minutes for the same batch, and with remarkable precision. I even integrated a perfectly functional M3 thread directly into the print, with no need for tapping afterward. The jigs are now validated, with a dimensional deviation of less than 0.05 mm.”
– Arnaud Teissonnier, Design Office Manager at HTI Technologies
About HTI Technologies
HTI Technologies established in 1979, specializes in bioceramics, medical coating, and medical packaging solutions. It specializes in providing innovative solutions for wear constraints in industrial applications. Today, HTI operates two manufacturing sites in France and has subsidiaries in Turkey and the United States, serving a diverse range of industries, with over 50% of sales generated from export.
Traditional Process and Limitations
“In our business, we use fixtures for gripping and positioning very small, precise parts, particularly for machining or marking operations.”
HTI relied on CNC machining for creating fixtures used in gripping and positioning small, precise parts for machining and marking operations. While CNC machining offered excellent precision, it was costly and time-consuming, often requiring 1 to 3 weeks for production.
Later they introduced FFF 3D printing which reduced lead times but lacked the necessary precision for certain fixtures.
HTI primarily used PVC and ABS for fixtures due to their ease of shaping, and good mechanical properties, and medical device compatibility. However, these materials and processes still presented limitations in efficiency and cost-effectiveness.
The Need for a High-Precision 3D Printer
HTI was already familiar with 3D printing but required greater precision than what FFF machines could provide. The Raise3D DF2 resin DLP printer, along with its complementary DF Wash and DF Cure, offered the accuracy needed for their operations. The Digital Light Processing (DLP) technology of the DF2 provided superior print resolution, significantly improving the production of fixtures.
Key Benefits of Raise3D DF2
- Precision & Speed: The DF2’s accuracy addressed the precision gap left by FFF printing. Additionally, its higher print speed reduced the time required for iterations and validations, shortening the period between initial inquiries and commissioning.
- Efficient Batch Printing: Unlike FFF methods, the DF2’s “printing time depends on the height of the part and not on the number of parts on the plate, so we can test different combinations in an average of 3 hours, whereas it used to take us at least 12 to 24 hours.”
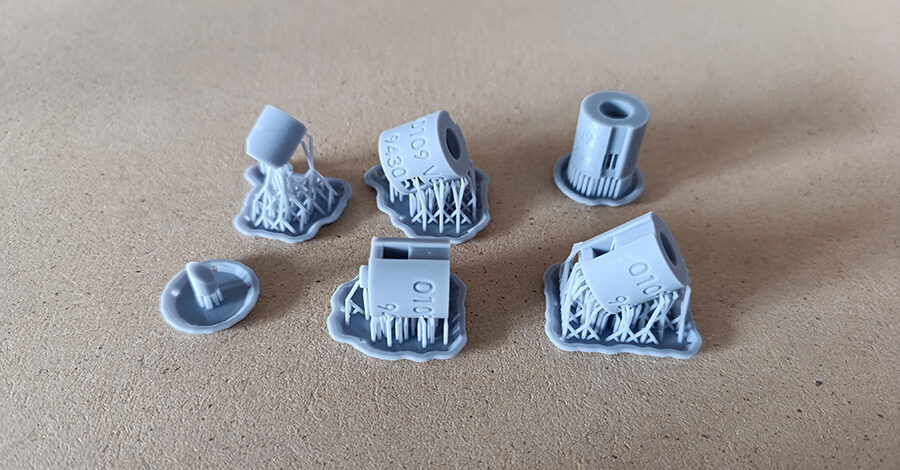
Image of a batch of laser marking jigs, with different orientations and tolerances, in order to determine the optimal parameters for the production of a set covering the entire product range.
Why Raise3D?
After benchmarking different market options, HTI selected Raise3D for several reasons:
- Ease of Printing & Post-Processing: The DF2, combined with DF Wash and DF Cure, simplified workflows and post-processing by leveraging its RFID technology, which ensures a fully traceable and efficient process from start to finish.
- Material Flexibility: “Wide choice of materials, thanks to its openness to third-party materials (Henkel Loctite, Forward AM, etc.), enabling it to cover a wide range of applications, with the integration of profiles tested by Raise 3D in ideaMaker”.
- Dimensional Accuracy: The DF2 consistently met HTI’s stringent precision requirements, ensuring high-quality results.
Implementation and Results
“For the time being, we are using Standard and Tough 2K resins, the latter meeting our needs and offering similar advantages to the materials previously used.” The company plans to expand into more technical resins as their needs evolve.
Key Outcomes
- Faster iterations: Fixture validation time reduced from 12-24 hours to 3 hours.
- Improved precision compared to FFF.
- Reduced costs and lead times compared to CNC machining.
- Laser marking jigs validated with a dimensional deviation of less than 0.05 mm
Software Integration
HTI uses Raise3D’s ideaMaker software for its seamless integration with the DF2. ideaMaker’s pre-generated print profiles streamline the printing process, minimizing back-and-forth adjustments. “The advantages of this slicer for the DF2 are its range of very practical functions (hollowing out parts, modifying textures, etc.) and access to advanced settings, allowing you to fine-tune each print.”
Conclusion
HTI Technologies is highly satisfied with the Raise3D DF2 printing suite, as it fully meets their operational requirements. The combination of precision, speed, and material versatility has significantly improved their workflow efficiency.
By adopting the Raise3D DF2, HTI Technologies has overcome the limitations of traditional fixture production methods. The integration of high-precision 3D printing has streamlined their processes, reducing lead times and costs while improving overall accuracy. As HTI continues to explore more technical resins, Raise3D’s open-material approach ensures their evolving needs will be met.
We would like to extend our sincere appreciation to HTI Technologies and Arnaud Teissonnier, Design Office Manager at HTI Technologies, for their valuable insights and contributions to this case study. Their expertise and detailed feedback were instrumental in highlighting the benefits of 3D printing with Raise3D.