Sonmak Diamond Tools is a company that produces diamond-cutting tools for the natural stone industry. They manufacture cables for extracting blocks from mines, gangsaws for dividing these blocks into slabs, and saws of different diameters for cutting plates. As a leading cutting tools manufacturer, Sonmak Diamond Tools uses the Pro2 Plus from Raise3D to apply 3D printing for customization on its production line.
Obstacles encountered when manufacturing parts without 3D printing
During production, the wide range of parts required and the production process itself could, on occasion, cause issues. As a result, the Sonmak team needed to design and manufacture the required parts independently, which can be complex and costly. They originally used traditional machining methods to produce parts and tools. For example, their machine was designed to polish the surface of materials with variable angles and corners, but they found that it was difficult to manufacture. It would take a lot of time to produce this kind of machine. The team encountered more obstacles, especially when producing complex parts.
For these reasons, the Sonmak team began to produce these parts on the Raise3D Pro2 Plus 3D printer, because it can easily print parts designed with any geometry.
3D printing meets customization and high-intensity needs
During packaging, the team wrapped the edge of the saw with a printed cover so that the saw would not damage the packaging during transportation. Different sized saw edges required a corresponding packaging cover, and this meant the team needed to create differently sized covers in small quantities. A 3D printer can meet the customization needs of each cover. The size and specifications of the printing cover can be adjusted to whatever is specifically required at the time.
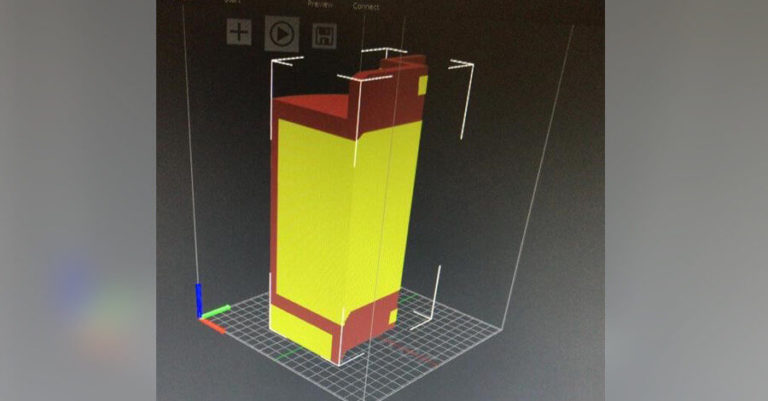
Sonmak designed and sliced models in ideaMaker.
Another example is a suction system Sonmak printed to remove dust from their machine, to prevent the dust from spreading into the environment. These parts were mounted on a high vacuum cleaner and moved with the machine knife to prevent dust leakage. It was a creative solution to solve a pain point of the production process. 3D printers are excellent tools for increasing productivity, providing production freedom, speeding up product development processes, and lowering costs. By utilizing desktop 3D printers in the production line, the company managed to overcome many problems and these processes have become easier. A 3D printer can quickly produce a solid part from a design.
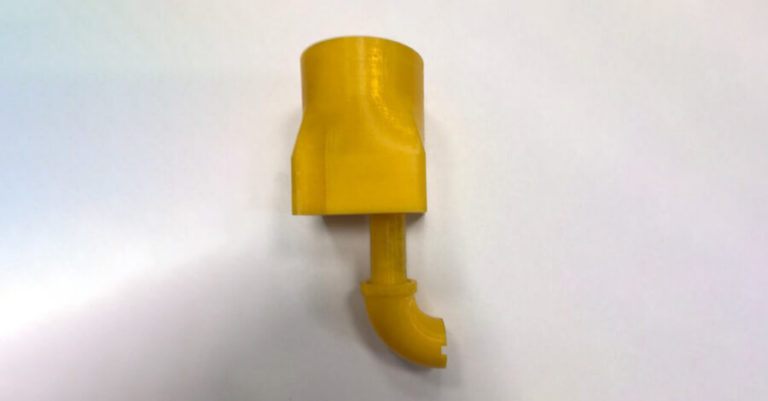
Sonmak used Raise3D Pro2 Plus 3D printer to print a set of a suction system, which greatly protected the working environment.
Advantages from Raise3D Products for Process Improvement
Sonmak Diamond Tools used the large-volume Raise3D Pro2 Plus 3D printer with a 12×12×23.8 inch (305 x 305 x 605mm) build volume. The large manufacturing volume adds more value to the company, especially when manufacturing objects for machine parts production.
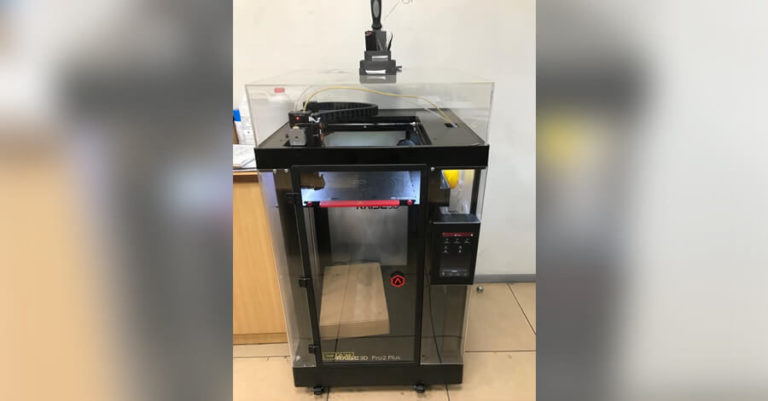
Sonmak Diamond Tools use their large-volume Raise3D Pro2 Plus 3D printer to increase tool production efficiency.
With the help of ideaMaker, the capability of 3D printers is not limited by the ability of the designer. With the help of algorithm, ideaMaker is well integrated with our printer. When Sonmak Diamond Tools needed hooks of different sizes to apply to stones of different shapes, the team designed hook model files and used Raise3D slicing software, ideaMaker, to process them with the optimal algorithm. The combination of the two enabled the 3D printer to quickly establish a complete printing scheme.
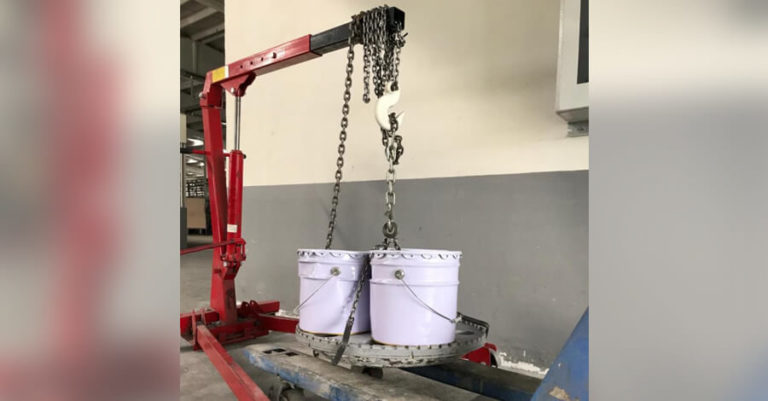
The hook printed by Raise3D Pro2 Plus 3D printer can bear a weight of 350kg.
Therefore, parameters of ideaMaker can help users achieve a rich product performance.

A station built to be able to test and keep the Raise3D printer‘s tools in order during the first days after the 3D printer came to the office.
3D printing improves traditional manufacturing iteration
3D printing can be used to manufacture parts with complex designs simply. 3D printing is a different method from traditional manufacturing and can replace CAD-CAM production. Mastering 3D printing technology can convince users of its convenience in professional manufacturing, and more importantly, increasing users’ 3D printing experience.
This case is shared by Raise3D’s Turkish distributor, 3dörtgen.