The Department of Otolaryngology at Zhongshan Hospital, affiliated to Fudan University (hereinafter referred to as „Zhongshan Hospital“), has successfully treated a child with a rare congenital bilateral anterior nasal atresia for the first time on a global scale. In this groundbreaking medical procedure, the team pioneered the use of 3D printing technology to design and validate a personalized anterior nasal support prototype for the patient.
In this innovative medical practice, the Raise3D team utilized the DF2 series DLP 3D printer to print high-precision medical prototypes, achieving rapid prototyping and validation of the stent. This provides critical technical support for the Zhongshan Hospital team in formulating the subsequent treatment plan.
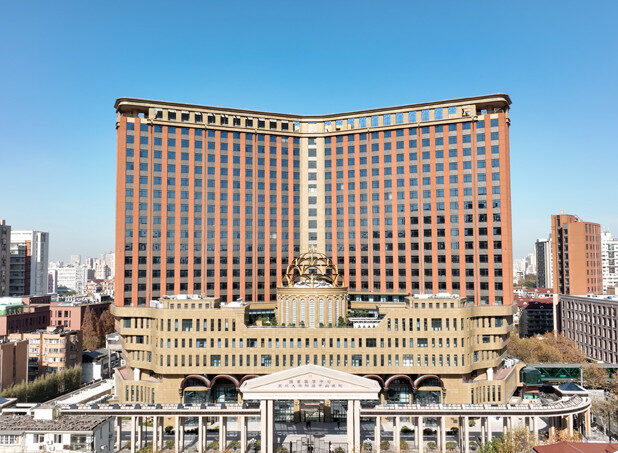
Zhongshan Hospital, Fudan University. Image source: Official website of Zhongshan Hospital, Fudan University (https://www.zs-hospital.sh.cn/zhuanye/)
A Rare Case, Bringing New Challenges
Zhongshan Hospital is China’s first comprehensive national medical center. Dr. Yu Haoran, a current member of the hospital’s otolaryngology team, once treated a special pediatric patient born with completely closed bilateral anterior nostrils, with only tiny pits remaining. This condition is extremely rare, and has no successful treatment cases reported worldwide.
The main challenge in treating this disease is the patient’s underdeveloped nasal alar cartilage and nasal appearance. Even if surgery is performed to open the nasal cavity, the surgical cavity tends to close quickly without structural support. Traditional methods used for posterior nasal atresia—such as inserting a tracheal or drainage tube—would cause strong discomfort, impair nasal function, lower quality of life, increase caregiving difficulty, and raise the risk of infection or necrosis. At the same time, the treatment team also noticed that there is still a gap in the market for nasal stents suitable for infants and young children, and there is a lack of reliable solutions.
Thus, the team faced the urgent challenge of developing an entirely new customized solution in a short period of time.
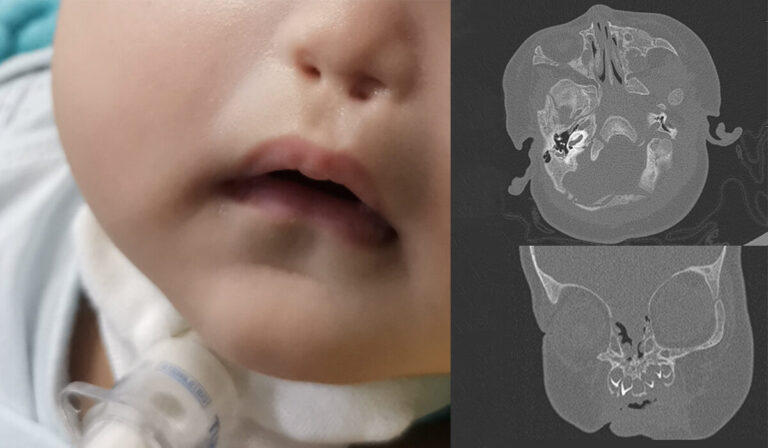
Left: The patient with nasal atresia who had to undergo emergency tracheotomy for ventilation; Right: CT image of the patient’s nasal area.
Image source: Zhongshan Hospital team
3D Printing Enables Rapid Customization
After a multidisciplinary team (MDT) discussion with plastic surgery experts and with the support of the „Fu Qing Scholar“ Scientific Research Innovation Project Fund from Fudan University Shanghai Medical College, the team decided to use 3D printing technology to customize an individualized nasal stent prototype for the patient.
The advantages of 3D printing were fully demonstrated in this case:
- Rapid Response: 3D printing technology supports high-frequency, rapid prototyping, and validation to meet urgent medical needs.
- High Customization: Designs can be tailored to the patient’s unique anatomy.
- Low-Cost Prototyping: Compared to traditional manufacturing, 3D printing is more cost-effective.
- Pandemic Flexibility: During the COVID-19 pandemic, the conditions for prototype validation in hospitals were limited, and 3D printing technology provided a flexible solution.
Based on these advantages, Dr. Yu contacted Raise3D’s China branch and learned that Raise3D is developing a new DLP 3D printer – Raise3D DF2. The DF2 is a DLP 3D printer with stable performance and high printing accuracy, supporting a variety of resin materials. At the same time, the Raise3D team has excellent printing service capabilities, responds quickly, assess customer needs, and provide the most suitable solutions for users.
All parties agreed to use the DF2 for the prototype design and validation of the nasal stent.
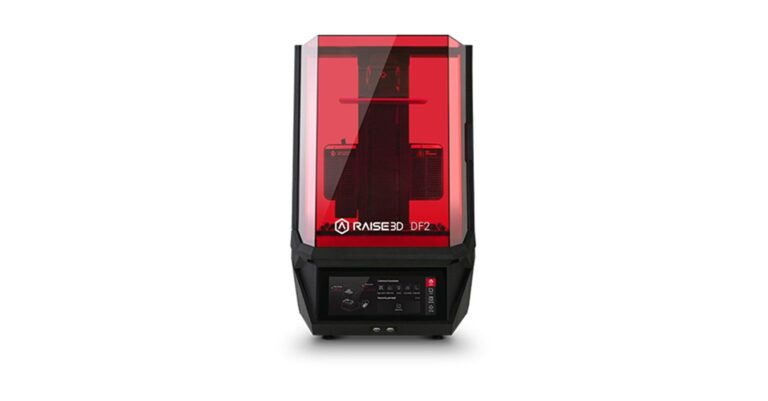
Raise3D DF2 3D printer
Efficient Workflow with Raise3D DF2 Series
Upon receiving the request, the Raise3D team conducted a detailed evaluation. Taking comfort and biocompatibility into consideration, the team selected the flexible resin material – Forward AM Ultracur3D® EL 60 after multiple trials for this prototype validation work.
The entire post-surgical support process lasted 15 months. During this period, the Zhongshan Hospital team and the Raise3D team worked closely together and iterated the stent design multiple times to fit the patient’s nasal shape and different usage scenarios.
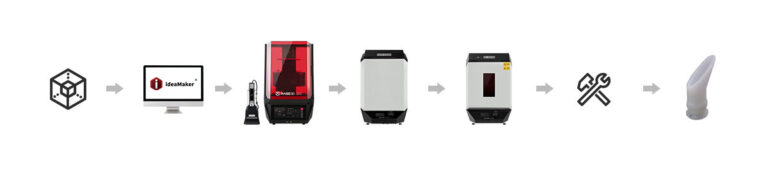
3D printing stent process diagram: Modeling – Slicing – Printing – Washing – Curing – Post-processing – Finished prototype
Raise3D’s self-developed ideaMaker slicing software, with its powerful DLP slicing function and fast slicing speed, ensured the rapid slicing of the model and provided a guarantee for smooth printing.
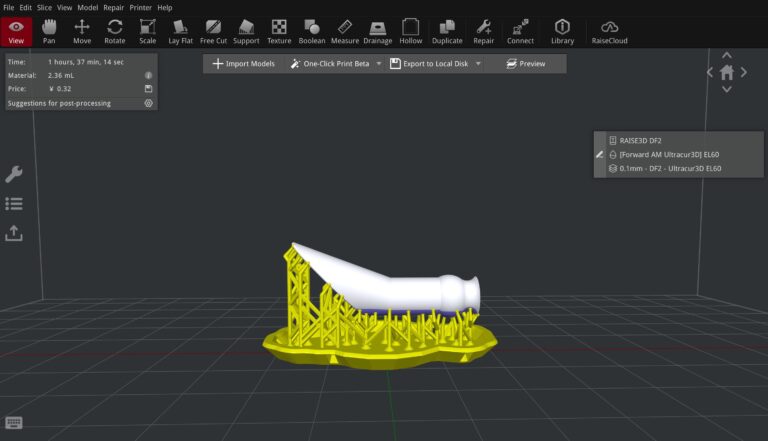
ideaMaker slicing software illustration
After slicing, the Raise3D team used the DF2 DLP 3D printer to print the stent prototype. The DF2 uses DLP technology to achieve high-precision printing, suitable for fine prototype making. At the same time, the professional printing service level and capabilities of the Raise3D team ensured the rapid response and scheduling of printing needs, ensuring that each delivered piece met user requirements. Through the perfect combination of service capabilities and equipment, the Raise3D team achieved multiple design iterations of the stent on the same day.
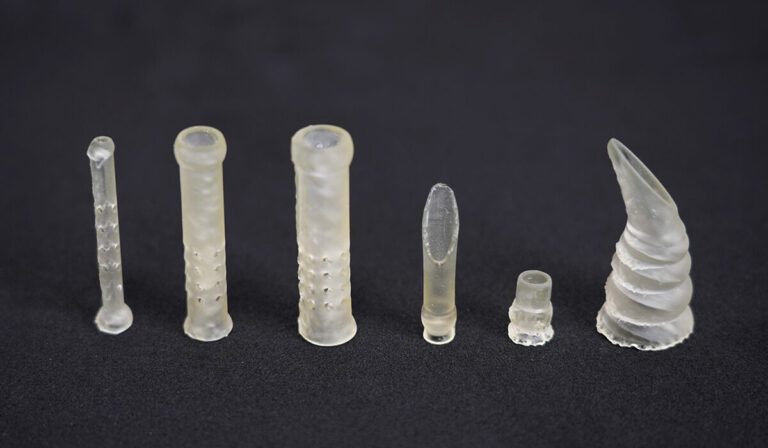
Stent prototype printed with Raise3D DF2 printer
After printing, the model was quickly washed and cured through the DF Wash and DF Cure. RFID technology automatically transmits setting parameters throughout the printing, washing, and curing process, without manual intervention, further improving efficiency.
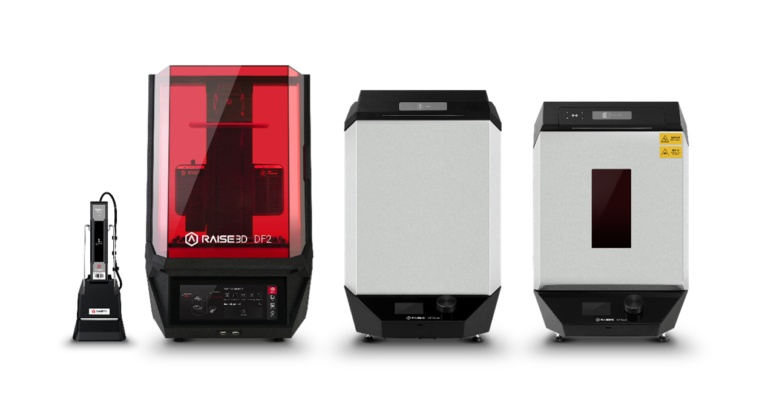
Raise3D DF2 Series Solution, including DF Wash and DF Cure
Raise3D’s DF2 series solution—including post-processing equipment—enabled fast, cost-effective, and frequent prototype iterations, helping the hospital team finalize the optimal design.
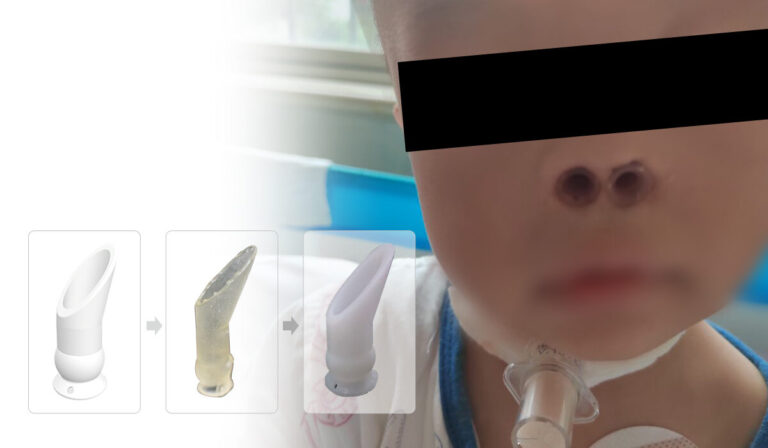
Model – prototype – finished part, and the patient wearing the finished part in the nasal cavity. Image source: Zhongshan Hospital team
Following the surgery and three months of progressive improvement, the patient gradually regained the ability to breathe nasally through the tube, exerting normal nasal function, and the physical and language development were sound. The customized stent has good concealment, high fit, strong comfort, and is easy to care for. The patient quickly learned to remove and wear it, resuming a normal life.
This case is just one example of how Raise3D supports scientific research and innovation in the medical field. Technology serves both the collective needs and individual well-being.
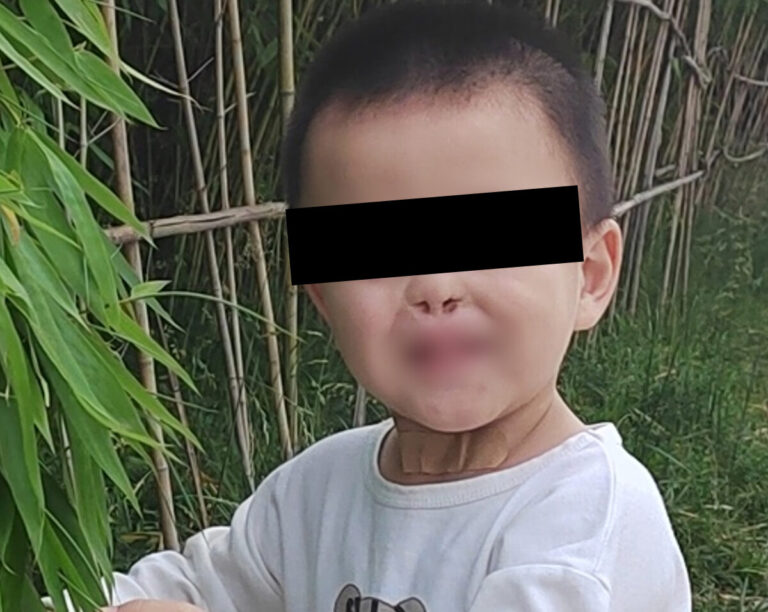
Current status of the patient. Image source: Zhongshan Hospital team
This year, Raise3D officially launched the new model of the DF2 series printer – the Raise3D DF2+ globally. The DF2+ provides industrial-grade precision, stability, and reliability. With a printing speed of up to 100 mm/h, it is very suitable for rapid prototyping and small batch production that can complete multiple design iterations in the same day. Compared to the DF2, the DF2+ can adapt to more high-performance resins, thus unlocking a broader range of applications for users and supporting every innovation.
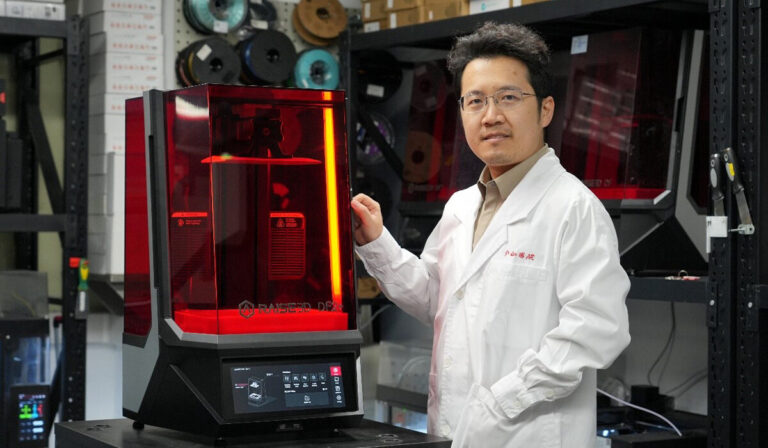
Dr. Haoran Yu from the Otolaryngology team of Zhongshan Hospital, Fudan University with Raise3D DF2+ 3D printer
Unlocking Possibilities with Medical 3D Printing
This successful case once again proves the great potential of 3D printing technology in the medical field. In the global first, time-urgent case treatment plan design, rapid and low-cost 3D printing technology has become the preferred tool for medical workers. The Raise3D DF2 series printer, with its high printing speed and accuracy, continues to innovate in the field of medical prototype validation and bring benefits to more patients.
If you have customized service needs in the medical or other application fields, please feel free to contact us for professional evaluation and technical support.