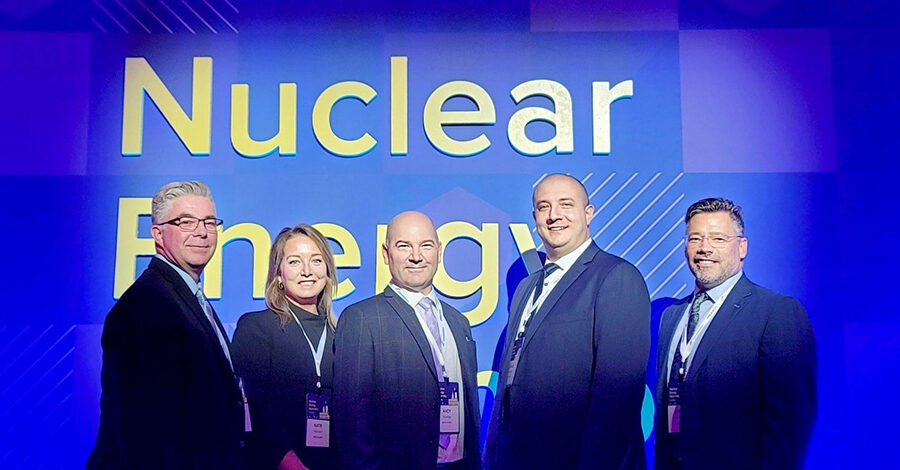
Nuclear energy company Bruce Power has been awarded a Top Innovative Practice (TIP) Award. Left to right: David Campbell, Katie Merchant, Andy Rutledge, Michael Bonaventura, and Chief Nuclear Officer Chris Mudrick
On September 10, 2024, at the Nuclear Energy Institute (NEI) Nuclear Energy Conference in Philadelphia, nuclear energy company Bruce Power has been awarded a Top Innovative Practice (TIP) Award for a novel approach to in-station radiation safety that leverages tungsten-infused filament and Raise3D 3D printing technology.
About Bruce Power
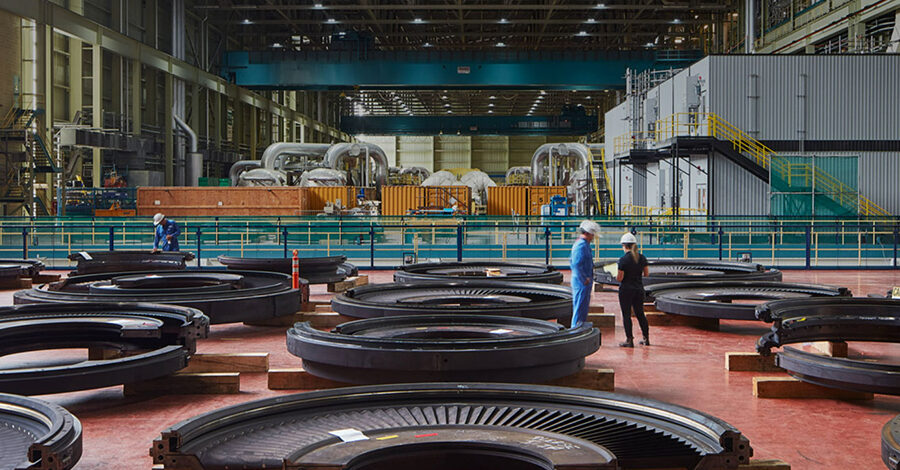
Bruce Power factory
Bruce Power is an electric utility headquartered in Bruce County, Saugeen Ojibwe Nation, Ontario, Canada. Bruce Power was founded in 2001, providing over 30% emissions-free, low-cost, reliable power with nuclear power to Ontario homes and businesses, as well as cancer-fighting medical isotopes to the world.
Challenges Faced by Bruce Power
The project at Bruce Power began in March 2023. Bruce Power’s engineering team wanted to accelerate the prototyping of custom shielding parts using tungsten filaments to manufacture each part, which could weigh up to 30 pounds. When choosing a 3D printer, the team had a series of demanding requirements. They needed a 3D printer that:
- Could produce custom shielding parts with complex structures, such as valves, camera equipment, and elbows.
- Enabled parts to be developed, printed, and installed to the target hot spots within several days.
- Could efficiently produce models in batches.
- Was compatible with tungsten filament.
- Had a footprint similar to that of an ordinary office copier and could be used indoors.
With these requirements in mind, they came to the showroom of Raise3D’s Canadian sales partner Shop3D.ca, seeking a printer with stable performance and efficient production.
Usually, such high requirements demand a high budget, but based on Shop3D.ca’s experience with similar materials (such as 316L stainless steel with a binder), they recommended the Raise3D Pro3 Printer, a solution that was both feasible and within their budget.
Application of Pro3 Printer in Prototyping of Custom Shielding Parts
- Rapid Custom Prototyping for Installation within 48 Hours
Compared to traditional custom shielding manufacturing methods, the Pro3 printer can quickly complete prototypes, allowing for faster iterations and design improvements. As long as the R&D team prepares the 3D printable file and sends it to the printer, the model can be printed with one click. Bruce Power notes that with the Pro3 printer, they can develop, model, print and install the model to the target hotspot within 48 hours. This greatly reduces time and customization costs.
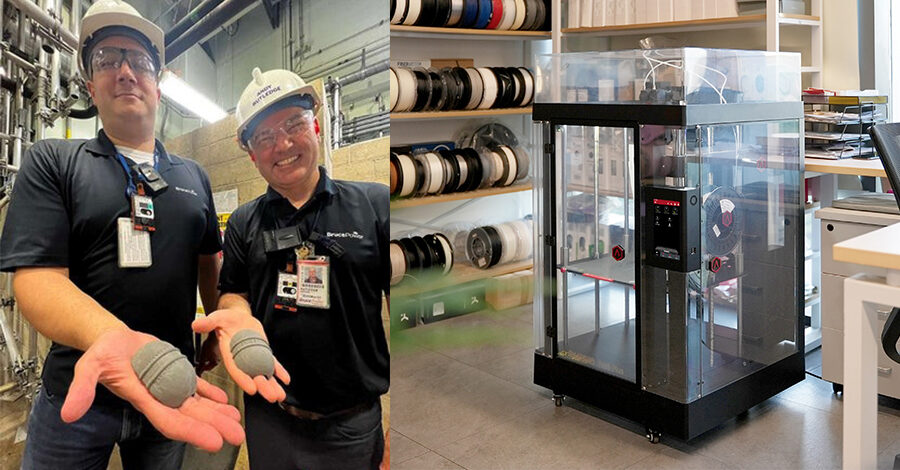
Model printed by the Bruce team
- High Printing Stability Provides Good Part Quality
Finding a balance between high-speed printing and high-quality results is a challenge, but the Raise3D Pro3 printer is designed to maintain good part quality at high speeds. The Pro3 printer can print complex valves, camera equipment or curved pipes with micron-level accuracy and good physical properties, providing an additional protective barrier for the space station.
Bruce Power needs to print with tungsten filaments. Although tungsten filaments will wear the nozzle and the mechanical structure of the printer, the models printed by the Pro3 printer are ensured to have a high durability. This is thanks to the enhanced mechanical structure of the Pro3 printer. The Pro3 printer body adopts an all-metal frame to ensure that the machine slides smoothly during printing and ensures the accuracy of printing. The Z-axis rod of the Pro3 printer is 75% stiffer, and the reinforced build platform and nozzle wear-resistant upgrade ensure more stable printing performance.

Enhanced printing platform, nozzles and structure of Raise3D Pro3
- Large Model Customization and Mass Production
Due to the complexity and diversity of customized shielding parts, Bruce Power sometimes needs to produce parts weighing up to 30 pounds. The Pro3 printer has a build volume of 300x300x300mm (the Pro3 Plus has a build volume of 300x300x605mm), which can meet the needs of rapid prototyping and large-scale production of large models. Bruce Power says that once they have made a model of a custom part, they can gain additional efficiency by using the same template for the same components throughout Bruce Power’s eight units . The high repeatability of the Pro3 printer ensures that each batch of models maintains a uniform print quality.
- User-friendly Experience and Low-waste Production
The Pro3 printer does not require any installation conditions and usage restrictions, and can work quietly in any workspace in the classroom or office. The Pro3 printer will not produce waste that pollutes the environment, which is in line with Bruce Power’s concept of a clean community.
- Large-scale Deployment to Improve Production Efficiency
The ecosystem supporting the Pro3 printer includes the free slicing software ideaMaker and the cloud management platform RaiseCloud, which helps Bruce Power deploy multiple printers throughout the factory and achieve unmanned, online monitored, 24/7 all-weather production. The ability to do this greatly improves production efficiency and promotes the rapid implementation of projects.
« Bruce Power’s 3D tungsten shielding project is easily replicable across the nuclear industry and is a great example of our team using innovative thinking to improve safety, » said Chris Mudrick, Bruce Power’s Chief Nuclear Officer and Executive Vice President. « Our team took this project from concept to prototype in just 30 days, and completed field testing and approval for application across the nuclear power plant in 90 days. I congratulate the team for all their hard work in making this vision a reality. »
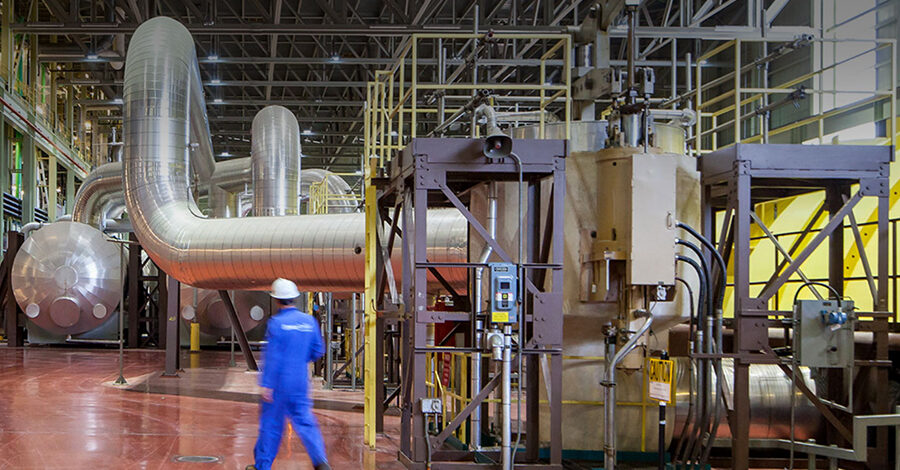
Bruce Power factory
Bruce Power Project Success with Pro3 Printer
With the help of the Raise3D Pro3 printer, Bruce Power was recognized with a Top Innovative Practice (TIP) Award for a new approach to radiation safety at the station using 3D printing technology and tungsten filament.
This approach enabled their team to achieve a level of precision and flexibility in their application that was unprecedented in the field of radiation shielding at nuclear facilities. “This approach can serve as a model for the entire industry to use existing technology in innovative ways,” said Chris Mudrick.
Raise3D and Shop3D.ca congratulate the Bruce Power team on receiving a well-deserved Top Innovation Practice award! We are proud to be a part of your journey.
This case is shared by Shop3D.ca, which is Raise3D’s reseller in Canada.
References
https://shop3d.ca/blogs/news/bruce-power-wins-award-for-new-3d-printed-radiation-shielding