Users who are familiar with the world of additive manufacturing (AM) will not be surprised to hear about items of clothing made using 3D printing. But for those who are not aware, it is an area where 3D printing has enjoyed a lot of success.
3D-printed footwear represents a revolutionary leap in the world of shoe design and manufacturing. It can create customized and highly intricate shoe structures, and unlike traditional methods, 3D printing allows for unparalleled precision, enabling the fabrication of shoes tailored to the unique contours of an individual’s feet.
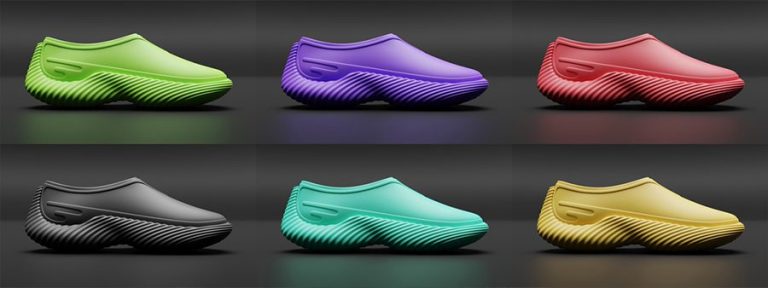
3D-printed footwear represents a revolutionary leap in the world of shoe design and manufacturing.
Additionally, 3D-printed footwear promotes sustainability by minimizing material waste and enabling the use of eco-friendly materials.
So, it is no surprise that this type of manufacturing has been developed and explored within the AM community. Crea3D, a Raise3D reseller based in Italy, and FastParts, an AM service company from within Crea3D’s ecosystem, developed the FuSa shoe, a custom sneaker with a range of unique properties.
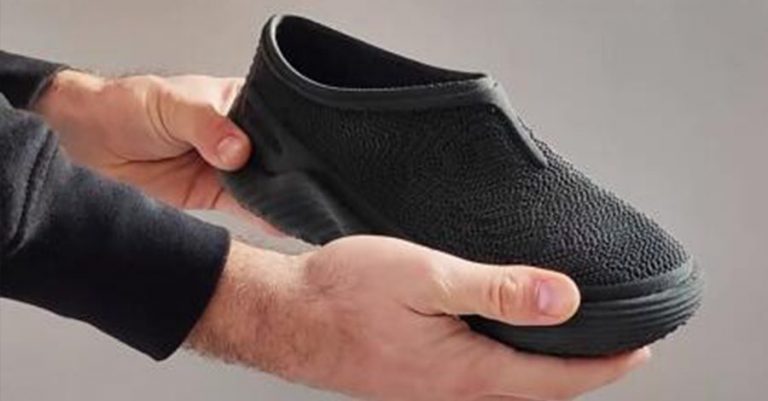
3D-printed footwear promotes sustainability by minimizing material waste and enabling the use of eco-friendly materials.
The FuSa shoe was given its shape by the designer Fabrizio de Lucia, and the name “FuSa” comes from Fused Filament Fabrication technology and Sapato (« shoe » in Portuguese). FastParts were responsible for the initial fabrication, which was carried out on a Raise3D Pro3 using TPU, a flexible material commonly used for this type of object.
Further iterations of the FuSa reduced the weight of each shoe from over 500g to under 300g (using about 600g of material for the pair) and improved the flexibility. The versatility of 3D printing allowed for a shoe upper that was breathable, and the infill of the sole was modified for a better elastic response. At the same time, the wearability of the sneaker has also been improved, based on a size 42 (EU) shoe.
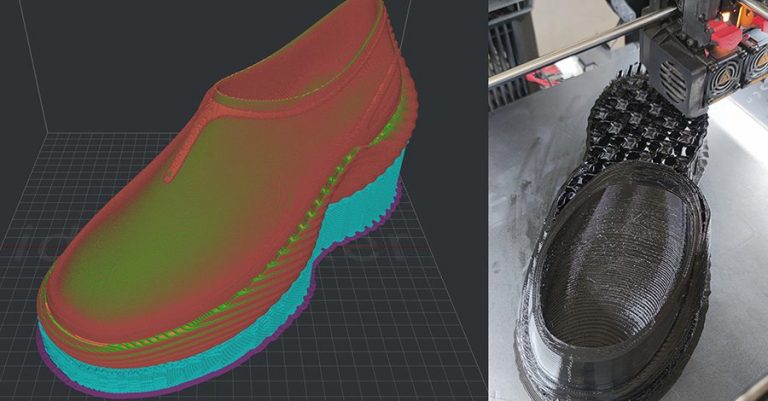
The name “FuSa” comes from Fused Filament Fabrication technology and Sapato (« shoe » in Portuguese).
Subsequently, the print was engineered to continue to be made in TPU but printed on the Raise3D E2 printer. New 100% recycled materials are being analyzed, and the topological optimization of the infill of the sole was subject to study. Raise3D’s software, ideaMaker, allows the team to modify infill patterns and even vary the density in different regions of the 3D model to be printed, making it a powerful tool for demanding objects such as the FuSa.
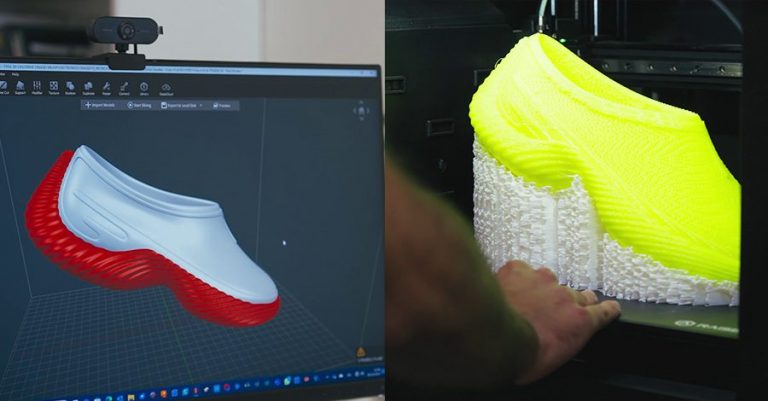
The print was engineered to continue to be made in TPU but printed on the Raise3D E2 printer.
The latest tests use a different type of TPU filament resulting in better flexibility and the aforementioned reduction in weight. The need for different materials can lead users to look for alternatives from various suppliers, and if so, they can rely on Raise3D’s ideaMaker library to provide printing profiles for third-party filaments for the best possible results.
Producing a pair of shoes using a 3D printer with IDEX (Independent Dual Extruders), a dual nozzle setup that comes with the Raise3D E2, takes about 24 hours. One nozzle creates the shoe in TPU, while the other provides the support material, which is PLA. At the end of the print, the removal of the support material is a quick and easy step, taking about 5 minutes.
FuSa is a great glimpse into the future of customised footwear, a future where what we use on our feet can be made to suit the contours of our body to a high degree, while supplying an amazing degree of comfort, flexibility and lightness.
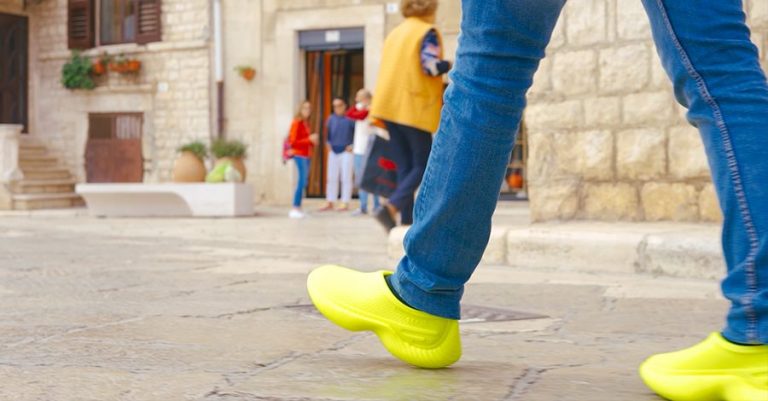
FuSa is a great glimpse into the future of customized footwear.
This case was shared by Crea3D , a Raise3D reseller based in Italy, and FastParts, an AM service company from within Crea3D’s ecosystem.