3D Printing is Making a Splash in the Field of Industrial Technology
Artitek provides professional CNC machining services, that mainly focus on motorcycle part design and manufacturing. The company uses 3D printing to make the prototyping process more efficient, and test out different design variations. According to Mr. Chen, the CEO of Artitek, the company had experimented with 3D printing before but was not satisfied with the results. However, after experiencing continued delays with the traditional CNC manufacturing process, Artitek returned to 3D printing, but this time with the Pro2 dual extruder 3D printer from Raise3D. This time, by using a professional 3D printer like the Pro2, Artitek was able to develop the “Artitek style” and successfully launch the company’s first product in 2021.
3D Printers Improve Efficiency in Product Development
Before 3D printing was introduced into the CNC industry, designers lacked visual verification tools. With trends and needs changing faster than before, the lack of verification tools widened the gap between design and manufacturing. This gap can extend the time it takes to finalize a design, meaning it is harder and takes longer to produce a final product.
Artitek experienced this frustration during prototyping. Prototyping is an important process because it enables the designers to see and test a physical model of a potential product. However, when the company used CNC machining, once the drafts were completed, the CNC machines were always occupied. Once the machines were finally ready for testing, designers waited weeks and sometimes even months for prototypes. The cycle would repeat itself if the designer needed to make alterations to the product. Artitek’s prototyping phase took at least two weeks, and the company’s entire conventional CNC manufacturing process took 5-6 months. Design trends can change dramatically in a few months, meaning the lengthy CNC manufacturing process could result in Artitek missing the right opportunity to enter the market with a specific design.
Wishing to shorten their prototyping phase, Artitek returned to 3D printing using the Pro2 dual extruder 3D printer from Raise3D. By going back to 3D printing, Artitek was able to complete a design and see a prototype in a few hours. Using professional 3D printers, like the Pro2, as validation tools before mass production saves a project time, money and improves efficiency. In the case of Artitek, their prototyping timeline was reduced to half a day, with the only cost being the filament to print the parts.
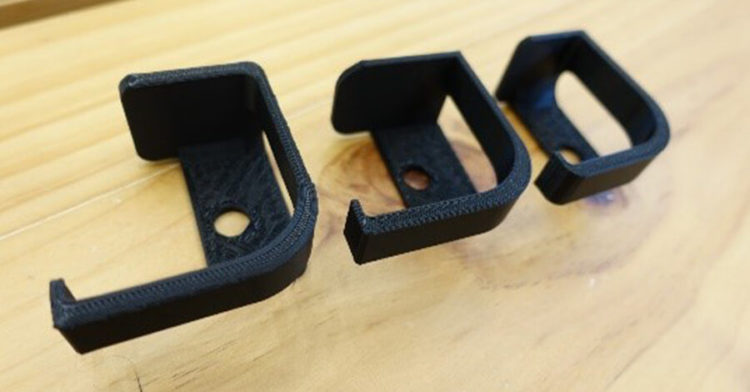
3D-printed prototype Prototypes within a week
Artitek Makes Flexible Use of 3D Printers
Manufacturers that use 3D printers can rapid prototype quickly and directly, especially when compared to traditional industrial production. This helps manufacturers, like Artitek, identify any opportunities where a design change is necessary.
For example, Artitek recently designed a brake lever. The company was able to detect the dimensional deviation of the first brake design because 3D printing enabled the company to produce and test parts within a few hours. The size of the brake handle is important because if the handle size is too big, customers with small hands cannot grab it comfortably. However, if the brake handle size is too small, it might lose strength. Both situations can endanger users because they may not be able to brake properly.
Artitek must make the right design decisions for the safety of their clients, and the Raise3D Pro2 helps the company make the right decision. The 3D printer connects to the slicing software, ideaMaker, establishing a perfect model design scheme. Due to the various functionalities of ideaMaker, Artitek was finally able to design a brake lever that achieves optimal mechanical performance with just a few parameter adjustments. The company can quickly view these adjustments on a physical model due to the efficient manufacturing nature of a 3D printer.
Motivated by the success of using the Pro2 in prototyping, Artitek expanded the use of the Pro2 dual extruder 3D printer to also print jigs and fixtures. The company designed a jig for laser engraving and found that 3D printing jigs and fixtures is convenient. Artitek was even able to produce the packaging material using the Raise3D Pro2 because the printer produces high-quality 3D printed parts.
Open Filament Program (OFP) Gives Artitek Better Options
Artitek does not print with one type of filament. The company uses different materials to match the strength and hardness requirements of different motorcycle parts. Artitek currently uses Raise3D’s Open Filament Program (OFP) to test nylon-carbon material. Raise3D’s Open Filament Program (OFP) aims to cooperate with the best 3D printing filament manufacturers so that more materials can be compatible, thus enhancing excellent print performance, better meeting customer needs. If the tests meet Artitek’s requirements, more will be put into future production. So, the OFP provides customers with performance parts for production use while building a bridge of cooperation and exploration with filaments.
Artitek will Promote 3D Printing Technology in the Future
Artitek plans to continue using Raise3D printers to improve design efficiency. The Pro2 printer from Raise3D is precise and stable, helping the company to produce new products quickly. Artitek is an example of how manufacturers that choose to utilize 3D printers to improve traditional production methods can get new products to the market quickly.
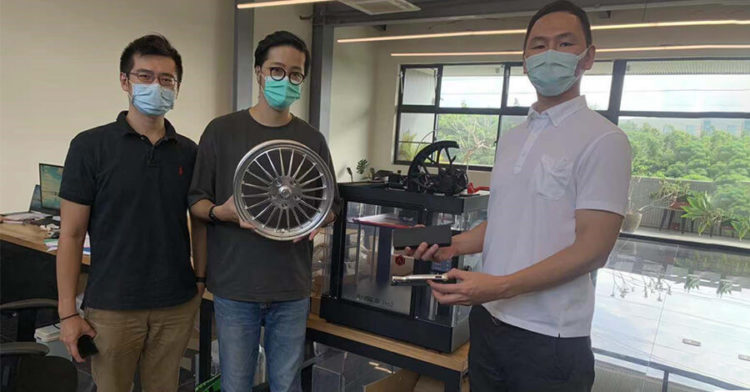
Artitek and Kiden Trading Ltd., Co
This case is shared by Raise3D’s Taiwan distributor, Kiden Trading Ltd., Co.